The cart is empty!
ICorr Coating Inspection Level 1 online
ICorr Coating Inspection Level 1 online
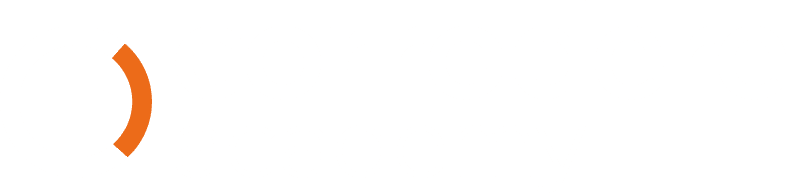
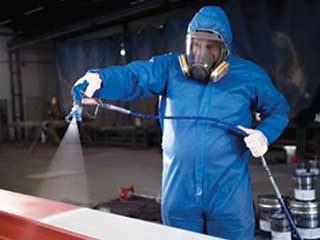
Course Overview
This comprehensive and flexible online course prepares candidates for the ICorr Coating Inspector Level 1 examination. It is suitable for candidates worldwide with at least 12 months of experience in the coatings industry. The course also includes an additional module focused on Marine and Offshore Coatings.
No travel or accommodation expenses – study from anywhere in the world.
Fit your studies around your work and family commitments.
ICorr Level 1 personnel are qualified to carry out operations in accordance with written instructions.
Level 1 ICorr Coating Inspectors are qualified to:
Set up and calibrate specific inspection or test equipment.
Perform tests and inspections according to written criteria.
Record and classify test and inspection results based on established criteria.
Accurately report the results.
Course details
Study time
40 hours online training, by a 1-day online practical workshop and 1-day online final examination.
Certificate/Qualification
ICorr Level 1 Coating Inspector Certificate of Achievement, valid for 5 years.
Entry criteria
12 months of coating or painting industry experience. To support your online learning programme, the training materials include videos, animations, voiceovers, and multiple-choice questions at the end of each unit.
Course fee
£900.00 – Course Fee
£175.00 – Online Exam Fee
£295.00 – Online Practical Workshop (mandatory)
Plus 20% VAT if applicable.
Course and examination enquiries
For any questions or further enquiries, please visit our training partner’s website at www.corrodere.com, or alternatively, you can contact them at:
+44 (0) 1252 732236
info@corrodere.com