The cart is empty!
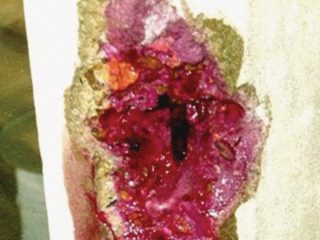
Ask the Expert
What Stops the Reinforcing Steel in Damp, Porous Concrete from Corroding (Usually)?
John Broomfield, Corrosion Engineering Solutions Ltd.
Meet the Author
John Broomfield
John Broomfield is a Fellow of ICorr, AMPP, and the Concrete Society. He is a Chartered Materials Engineer and Chartered Scientist. He is also a Level IV Senior Cathodic Protection Engineer and an AMPP/NACE International Corrosion Specialist. He has over 40 years of experience in dealing with deterioration and durability problems in the built infrastructure, specialising in reinforced concrete, corrosion of steel-framed structures, and conservation of historic buildings and monuments. He has worked on projects all over the world and undertaken condition surveys, repair feasibility studies, life cycle cost analysis, corrosion risk analysis, repair specification, and repair design. He specialises in the application of electrochemical techniques for the investigation, rehabilitation, and design of durable new construction.
Concrete
Concrete has been used for millennia in various forms, principally as unreinforced mass concrete. The Romans used a form based on volcanic ash extensively, one of the finest remaining examples being the Pantheon in Rome.
The development of Portland cement by Joseph Aspdin in the early 1800s using simple, widely available materials and then the development of reinforced concrete by François Hennebique in the late 1800s led to the development and use of reinforced concrete for buildings, bridges, and other major structures. There had been attempts to use other metals to reinforce concrete, but iron and steel turned out to be the most compatible due to the similarity of their thermal expansion coefficients [1].
Concrete is a composite of cement powder and water mixed with coarse and fine aggregates. It is the cement that binds the aggregates together as it hydrates. The most common binder is Portland cement, made from limestone and clay roasted and ground in a kiln. It is a complex mixture of calcium compounds such as silicates, aluminates, and iron oxides that, when combined with water, form a calcium silicate hydrate gel that binds the concrete mix together. The hydration process, when completed, leaves a level of porosity in the hardened concrete of the order of 10%. These pores contain calcium hydroxide both in solution and as a precipitate, along with some sodium and potassium oxides/hydroxides.
While strong in compression, concrete is weak in tension, requiring reinforcement in many applications. Steel exposed to water and oxygen will oxidise unless effectively starved of oxygen or completely dried out. Absence of water in concrete can occur in indoor environments or behind external cladding. Absence of oxygen can occur in submerged concrete. For normal outdoor exposure, the steel would be subject to corrosion at a rate that would be harmful over the lifetime of a structure due to the ingress of water and oxygen through the pore system unless otherwise protected.
Corrosion Resistance of Reinforcement
Fortunately, the excess calcium hydroxide in the concrete pores, combined with some sodium and potassium hydroxides, elevates the alkalinity at the steel surface to around pH 12.5 to pH13. At this point in the Pourbaix diagram [2], iron is passivated, forming a thin, protective, self-sustaining oxide layer with a very low corrosion rate. As long as the concrete cover to the steel remains intact, sufficiently alkaline, and uncontaminated, the steel will remain in good condition despite the presence of oxygen and water at the concrete and steel surfaces, or perhaps we should say that the protection of the steel is because of the presence of oxygen and water to maintain the protective passive oxide film. We therefore have reinforced concrete structures that can last 100 years or more without showing any signs of reinforcement corrosion.
A true passive layer is a very dense, thin layer of oxide that leads to a very slow rate of oxidation (corrosion). There is some discussion as to whether or not the layer on the steel is a true passive layer. It seems to be thick compared with other passive layers and it consists of more than just metal oxides but, as it behaves like a passive layer, it is generally referred to as such.
Corrosion scientists and engineers spend much of their time trying to find ways of stopping the corrosion of steel by applying protective coatings to steel. Metals such as zinc and polymers such as acrylics or epoxies are used to stop corrosive conditions from forming on steel surfaces. The passive layer is the corrosion engineer’s dream coating, as it forms itself and will maintain and repair itself as long as the passivating (alkaline) environment is maintained.
Factors that Accelerate Corrosion in Reinforcement
However, the passivating environment is not always maintained. For reinforced concrete in normal atmospheric exposure, two conditions can break down the passivating environment without attacking and destroying the concrete itself. One process is carbonation, and the other is chloride attack.
Carbonation occurs when the naturally occurring carbon dioxide (CO2) in the air reacts with the alkaline oxides/hydroxides in the concrete pore water. The dissolution of CO2 in water forms carbonic acid, a weak acid that does not attack the cement paste or the aggregates in the concrete but reduces the pore water pH below 10. At that point, the passive layer on the steel breaks down, and the steel is vulnerable to corrosion. Carbonation moves as a front through the concrete cover. The rate of progress of the carbonation front is approximated by a simple diffusion equation where the depth of carbonation x at time t after construction is given by:
x = kt1⁄2
Where k is a constant. The carbonation front is a transition in pH from about 12.5 to 8.5 and is a few millimetres wide. The depth of carbonation can be measured using an indicator solution, sprayed on to a freshly exposed profile through the cover concrete. An example is shown in Figure 1.
Right: Figure1: Phenolphthalein
Indicator Applied to Freshly Broken
Concrete to Measure the Carbonation
Depth on a Reinforced Concrete
Window Mullion.
The other condition leading to the de-passivation of steel is exposure to chloride ions (Cl-), generally from sea salt or de-icing salts. In this case, the chlorides diffuse into the concrete and build up in the concrete cover until there is sufficient concentration at the steel surface to break down the passive layer. There is no moving front, but there is a threshold for corrosion at the steel surface when the chloride ions successfully compete with the hydroxyl ions and break down the passive layer. The threshold is generally taken as being in the range of 0.2 to 0.4% chloride by mass of cement for low-alloy carbon steels in Portland cement- based concretes. It should be noted that for the newer “low carbon concretes,” the threshold has yet to be confirmed and may reduce with age [3].
Once the steel is de-passivated by carbonation or by chlorides, reinforcement in atmospherically exposed concrete will start to corrode. The most common corrosion process forms porous iron oxides with a volume several times that of the steel consumed. This leads to tensile forces which will crack and delaminate the concrete cover [4]. There are field techniques for measuring the carbonation depth in concrete and for sampling for chlorides. There are also non-destructive techniques for estimating the corrosion condition. Reference electrode potential measurements can identify areas of actively corroding steel and a polarisation resistance kit can estimate the corrosion rate [4,5].
Remedial Measures for Corrosion in Concrete
There are a range of techniques for preserving and restoring the passive layer on steel. These include the application of coatings, physical repair of the concrete, and a range of electrochemical techniques. Coatings are preferred for preventing the ingress of chlorides and CO2. BSEN 1504-2 [6] gives details on the selection and performance of anti-carbonation coatings and of penetrating sealers that resist chloride ingress. It has been found that anti- carbonation coatings are effective in controlling the corrosion rate in carbonated concrete by controlling moisture ingress as well as CO2 [7]. However, penetrating sealers applied to chloride contaminated concrete are less effective in slowing corrosion once the corrosion threshold chloride concentration has been exceeded at the steel surface.Electrochemical techniques such as re-alkalisation, chloride extraction, impressed current and galvanic cathodic protection are all effective in preventing corrosion of the steel, regardless of the extent of de-passivation if used appropriately [4].
Corrosion in Alternative Types of Concrete
It is important to recognise that the concrete cover to the steel must sustain the passive layer throughout the life of the structure if there is a corrosion risk. The performance of Portland cement concrete, and concretes with blended cements is well understood. However, there is now a new range of low-carbon cements being made available to the construction industry. In a recent article in CM [3], I expressed concern about the long-term corrosion protection afforded to low-alloy steel reinforcement by novel cement materials. Are there sufficient alkali reserves available over 50 to 100 year design lives to ensure the steel cannot corrode? Is anyone testing them? The recent problems with reinforced autoclaved aerated concrete (RAAC) are also interesting. RAAC is a very low-density concrete with minimal resistance to the ingress of water and CO2. It was designed for ease of handling and low cost. Much of the press-coverage around this issue is confused. RAAC has many problems and failure mechanisms and many are not corrosion related. These problems include poor placement of reinforcement, poor placement of units [bearing shelves], deterioration through wetting & drying cycles and negligible to zero cover to the reinforcement. However, RAAC was supposed to be used in a dry, indoor environment where the corrosion risk to the reinforcement is minimal. RAAC beams were often installed under flat roofing. Any leaks would expose the concrete to wetting and drying, which would allow rapid carbonation and rapid breakdown of the passive layer with subsequent reinforcement corrosion. Flat roofs have a limited life, and identifying leakage can be difficult, especially above false ceilings. The problems were foreseeable and were foreseen by many, but not necessarily always by those with the responsibility and budgets for keeping the buildings safe. Moreover, this is not just a corrosion issue or a failing of the material – if your roof is leaking, you have bigger problems than just how it might affect any RAAC that might be present.
Summary
We can therefore see that the alkaline reserves in the concrete pore water leads to the formation and maintenance of the protective passive layer on the reinforcing steel. This is crucial to the durability of steel-reinforced concrete exposed to normal atmospheric conditions. Those responsible for the maintenance of reinforced concrete structures need to understand how and why reinforcing steel is protected from corrosion. If corrosion occurs, the correct techniques must be used to assess the cause and extent of the problem and the correct treatment applied to control corrosion and maintain the asset for the required life.
References
- Paul Lambert Reinforced Concrete: The History, Properties and Durability of Reinforced Concrete , Technical Note 1 Corrosion Prevention Association, Bordon Hants, 2018.
- Pourbaix, M. (1974). “Applications of Electrochemistry in Corrosion Science and in Practice.” Corrosion Science Vol. 14: p. 25-82.
- Broomfield, J.P The Corrosion Resistant Properties of Novel Cements, Concretes, and Reinforcement, Corrosion |Management July/Aug 2023 pp 22-23.
- John Broomfield, Corrosion of steel in concrete, 3rd edition Publ. CRC Press, London, 2023.
- Concrete Society Technical Report 60, Electrochemical Tests for Reinforced Concrete. Concrete Society, Camberley, 2004.
- BS EN 1504-2 (2004) Products and Systems for the Protection and Repair of Concrete Structures – Definitions, Requirements, Quality Control and Evaluation of Conformity: Part 2: Surface Protection Systems for Concrete.
- Seneviratne, A. M. G., Sergi, G. Page, C.L. (2000). “Performance characteristics of surface coatings applied to concrete for control of reinforcement corrosion.” Construction and Building Materials 14: 55-59.