The cart is empty!
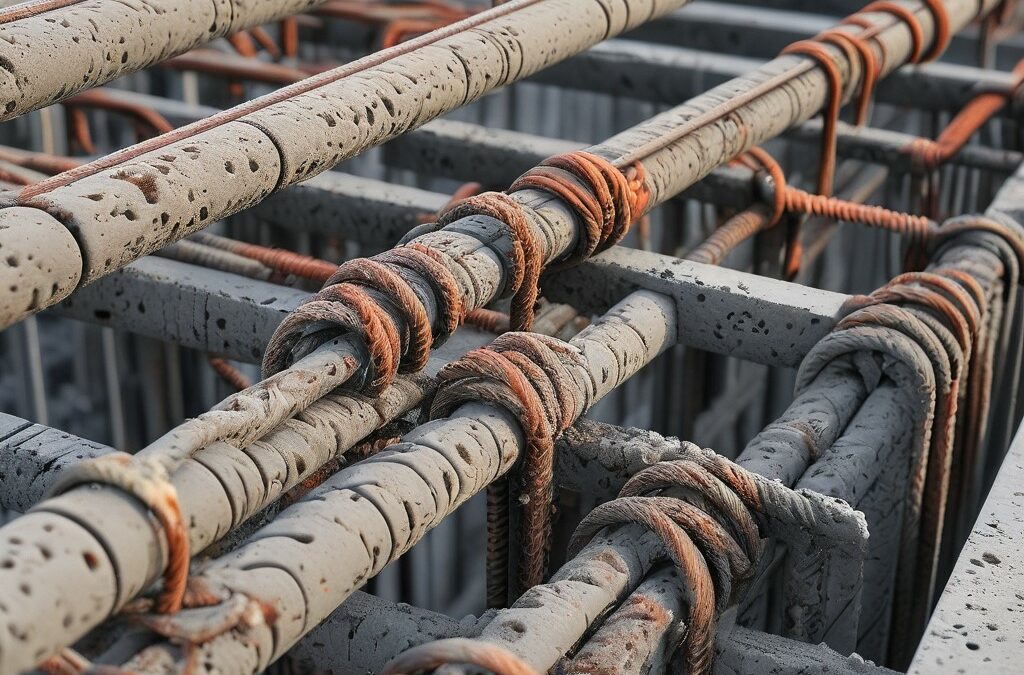
Advanced Techniques for Detecting and Mitigating Corrosion in Reinforced Concrete Structures
Understanding Corrosion Prevention in Concrete Structures
Corrosion in reinforced concrete is a pervasive issue that compromises the structural integrity and longevity of infrastructure. This phenomenon primarily stems from the deterioration of steel reinforcement within the concrete matrix. The resultant rust formation is bigger than steel, causing cracking, spalling, and eventual weakening of the concrete.
Failure to mitigate corrosion can lead to catastrophic structural failures, economic losses, and increased maintenance costs. Therefore, implementing advanced detection and mitigation strategies is essential for preserving the functionality and lifespan of these structures.
Mechanisms of Corrosion in Reinforced Concrete
Understanding the mechanisms behind corrosion in reinforced concrete is crucial for developing effective prevention and remediation strategies.
Corrosion in reinforced concrete is fundamentally an electrochemical process involving anodic and cathodic reactions. At the anodic sites, iron from the steel reinforcement oxidizes, releasing electrons. These electrons travel to the cathodic sites, where they reduce oxygen in the presence of water, forming hydroxide ions. This redox process results in the formation of iron oxides and hydroxides.
Two primary factors accelerate the corrosion process in reinforced concrete: chlorides and carbonation. Chlorides, often originating from de-icing salts or marine environments, penetrate the concrete and disrupt the passive oxide layer protecting the steel. Carbonation occurs when carbon dioxide from the atmosphere reacts with the hydrated cement paste, reducing the alkalinity of the concrete and allowing corrosion to initiate.
Advanced Techniques for Detecting Corrosion in Reinforced Concrete
Advanced detection techniques are crucial for identifying corrosion at its early stages, allowing for timely intervention. While tapping with a hammer can tell us much about the condition of a structure, more advanced detection techniques include:
1. Ground Penetrating Radar (GPR)
Ground Penetrating Radar (GPR) utilizes electromagnetic waves to identify anomalies within concrete structures. By analysing the reflected signals, GPR can detect areas of corrosion-induced damage, such as voids and delamination, without causing any damage to the structure. This non-destructive method offers a rapid and efficient means of assessing the condition of reinforced concrete.
2. Half Cell Potential Mapping
Half Cell Potential Mapping measures the corrosion activity in concrete structures. Concrete is removed around a suitable bar, and the resistance is checked between two separated points to determine a continuous flow of current. The area is mapped by taking readings across a grid of points, thus allowing us to assess for potential corrosion and the need for further investigation.
corrosion mapping is an effective method for assessing the severity of corrosion activity in concrete structures. It is the most well-known procedure to identify the likelihood of active corrosion; however, the test does not provide any information about the kinetics of corrosion activity.
Mitigation Strategies
Mitigating corrosion requires innovative approaches that address the root causes of corrosion in reinforced concrete and prevent further deterioration.
The most common method is Cathodic Protection, which controls corrosion by converting the anodic sites on the steel surface to cathodic sites. This is achieved by applying an external electrical current or by connecting a more easily corroded sacrificial anode to the steel. This technique effectively halts the corrosion process and prolongs the service life of the structure.
Another commonly used strategy is to add chemical compounds that act as corrosion inhibitors to the concrete mix or applied to the surface to impede the corrosion reactions. These inhibitors function by forming a protective film on the steel reinforcement, thus preventing the ingress of aggressive ions like chlorides. Various organic and inorganic inhibitors are available, each with specific mechanisms of action, though there is much debate as to how they work (repassivation or as a pore blocker).
Advanced Coatings serve as a barrier to protect steel reinforcement from environmental aggressors. These coatings, often comprising epoxy, polyurethane, or zinc-rich formulations, provide excellent adhesion and durability. The application of such coatings is a proactive measure to prevent the initiation and progression of corrosion – waterproof first, and worry about other things after.
Materials and Technologies in Corrosion Mitigation
The development of advanced materials and technologies is also proving critical in enhancing corrosion resistance in concrete strictures.
High-Performance Concrete (HPC) exhibits superior durability and resistance to environmental stressors due to its optimized mix design and enhanced material properties. The use of supplementary cementitious materials like fly ash, slag, and silica fume in HPC improves its impermeability, thereby reducing the risk of chloride ingress and carbonation.
Self-Healing Materials (such as NitCal) represent a another approach to corrosion mitigation. These materials can autonomously repair cracks and micro-damage within the concrete matrix through mechanisms such as autogenous healing, encapsulated healing agents, or microbial action. This self-repair capability significantly enhances the longevity and resilience of concrete structures.
Nanotechnology Applications in corrosion mitigation involve the use of nanomaterials to enhance the protective properties of coatings and concrete. Nanoparticles such as nano-silica, nano-clay, and carbon nanotubes can improve the mechanical strength, density, and durability of concrete, offering a robust defence against corrosive elements.
Future Directions in Corrosion Management
Several real-world examples illustrate the successful application of advanced corrosion detection and mitigation techniques. For instance, the use of EIS in monitoring the corrosion state of bridges in coastal regions (such as the Machico Stayed Bridge project in Portugal) can provide valuable data for maintenance planning. Similarly, the implementation of cathodic protection systems in historic structures has preserved their integrity for future generations.
However, the future of corrosion management lies in the continuous evolution of technologies and methodologies. In this regard, the importance of corrosion science cannot be overstated. Emerging research in the field of corrosion management is focused on developing more efficient and sustainable solutions. Innovations such as bio-inspired materials, smart monitoring systems, and environmentally friendly inhibitors will enhance corrosion resistance and extend the lifespan of concrete structures.
Though anode materials, monitoring devices etc have remained largely unchanged since the early 1990s, potential technological developments include the integration of artificial intelligence and machine learning algorithms to predict corrosion patterns and optimise maintenance schedules. Additionally, future advances in material science are expected to yield new high-performance composites and coatings with unparalleled protective properties.
By leveraging advanced detection techniques, innovative mitigation strategies, and cutting-edge materials, we can significantly mitigate the impact of corrosion on reinforced concrete structures. This requires a proactive approach that not only ensures the durability and safety of infrastructure but also contributes to sustainable development by reducing the need for frequent repairs and replacements.
The Institute of Corrosion’s (ICorr) Corrosion Science Division (CSD) is at the heart of promoting advances in corrosion knowledge and capability in the UK and around the world. Become a member of ICorr today and join the CSD to play your part in the scientific advance of the corrosion industry.