The cart is empty!
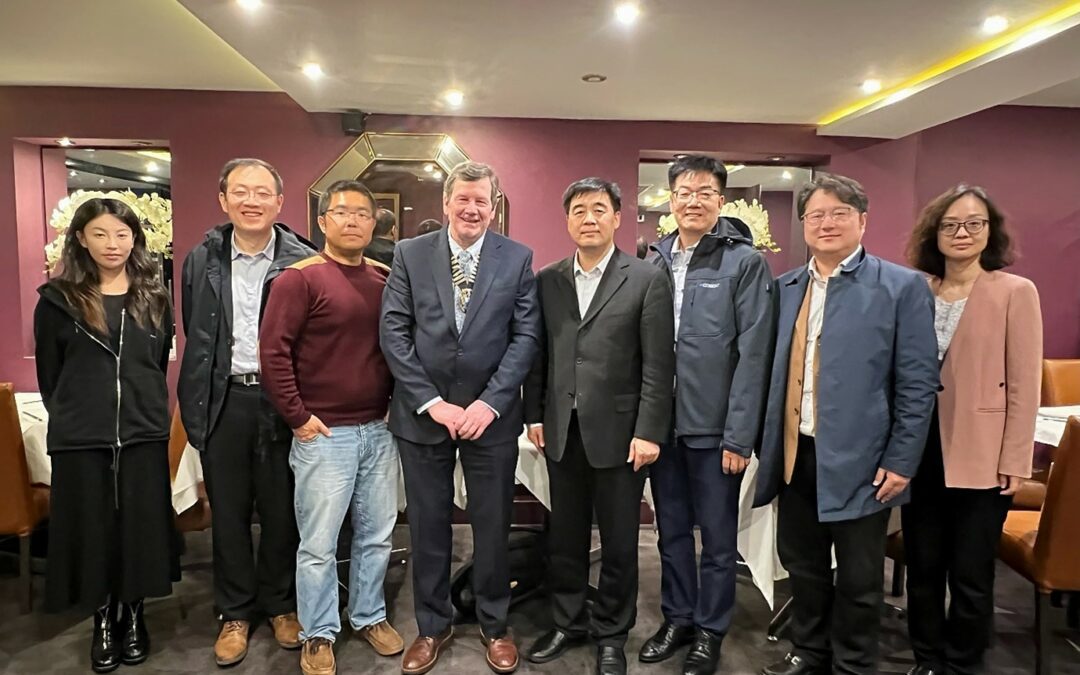
ICorr and University of Science and Technology Beijing (USTB) Collaboration Meeting in London
On Sunday 28th April 2024, the President (Stephen Tate) and Vice President (Yunnan Gao) had the greatest pleasure in meeting up with the delegation from University of Science and Technology Beijing, USTB, https://en.ustb.edu.cn/ the foremost University in China for Corrosion education. The London delegation was led by the Vice Chancellor and President of the University and formed of six people.
We have discussed a number of possible collaborative matters between ICorr and USTB going forwards.
In the September/October issue of Corrosion Management, Professor ZHANG Dawei, Director of Office of International Affairs, USTB, China will contribute a paper on the Application of Artificial intelligence and Machine learning in Corrosion management based on his recent research.
Also in October 2024, at the kind invitation of Chinese Society for Corrosion and Protection (CSCP) described below, Stephen and Yunnan will attend the 22nd International Corrosion Congress to be held on 22 – 26 October 2024 in Xi’an, China https://icc-corrosion.org/
The International Corrosion Council (ICC) on which ICorr is represented, was founded in 1961 to advance corrosion science and engineering represents 68 countries of the world including the UK and every three years organises the International Corrosion Congress.
Chinese Society for Corrosion and Protection (CSCP)
As an integral part of China Association for Science and Technology, the Chinese Society for Corrosion and Protection (CSCP) is registered in Ministry of Civil Affairs and is an academic organisation with independent legal entity in China. Founded in November 1979, CSCP currently has 7,979 individual members and 287 group members.
The 11th Council of CSCP comprises, Academician Baorong Hou, Academician Tongyi Zhang, Academician Shengkai Gong, Professor Guangzhang Chen, Professor Yu Zuo, Professor Lijie Qiao and Professor Fuhui Wang, who serve as the Honorary Presidents. Professor Xiaogang Li is the President, Professor Cuiwei Du et al are the Deputy President, Professor Xuequn Cheng is the Secretary-General.
CSCP consists of 7 working committees, 24 specialized committees and one standardization committee, and has 15 branches in Beijing, Shanghai, Liaoning and other provinces and cities in China.
The society is committed to building an academic exchange platform. The National Corrosion Congress, the Marine Corrosion Conference and the Electrochemical Corrosion Conference have become the brand conferences of CSCP. Each professional committee organises different forms of academic events every year. CSCP has also established several academic journals such as Journal of Chinese Society for Corrosion and Protection and Materials Protection.
CSCP carries out various kinds of popular science activities and publishes the popular science journal Corrosion and Protection Fan. It also issues scientific and technological awards to outstanding experts in the field of corrosion and protection at the National Corrosion Congress. Furthermore, it organises technical training and certification for corrosion engineers and enterprises, evaluation meetings for scientific and technological achievements, and provides consulting and other technical services for its members.
As an academic body, CSCP attaches great importance to the training of young corrosion scientists and engineers by organising Youth Corrosion Seminars and establishing Distinguished Academic Achievement Award for Young Talents.
The international organisations with which CSCP is affiliated include International Corrosion Council (ICC), Asia Pacific Materials and Corrosion Association (APMCA) and World Corrosion Organisation (WCO). CSCP has also formed long-term partnerships with AMPP International and European Federation of Corrosion (EFC) and will shortly complete the signing of an MoU with our own Institute (ICorr).
Agreements in Principle Made by Both Parties:
- To collaborate in the areas of training, joint webinars, conferences, ICorr membership and UK professional registration, including Chartered Engineer (CEng) and Chartered Scientist (CSci).
- To start the work to compose a formal MoU to document the agreements (to be formally signed at International Corrosion Congress).
- To hold the very first Webinar event later in 2024.
- To hold the regular joint Co-operation Meetings.
- To have alternating awards to outstanding ICorr and CSCP Members.
Photo: ICorr and University of Science and Technology Beijing (USTB) Collaboration Meeting in London on 28/04/2024
From Left to Right
- QIN Yuqing, Program Coordinator of Office of International Affairs, USTB, China
- Prof ZHANG Dawei, Director of Office of International Affairs, USTB, China
- Yunnan Gao, Vice President of ICorr, UK
- Stephen Tate, President of ICorr, UK
- Prof ZHANG Weidong, Vice President, USTB, China
- Prof ZHENG Wenyue, School of Materials Science and Engineering, USTB, China
- Prof XING Yi, Dean of School of Energy and Environmental Engineering, USTB, China
- ZHAO Meng, Director Office of Co-operation and Development, USTB, China.
Do please regularly check the ICorr Events Calendar for further details of upcoming activities www.icorr.org/events/