Ask the Expert, Uncategorized
Why is Effective MIC Control Still a Major Challenge for Many Oil and Gas Assets?
by Dr Ali Morshed, Consultant Corrosion Engineer, UK.
Meet the Author
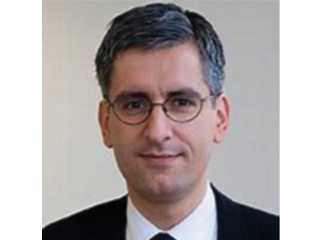
Dr. Ali Morshed
Dr. Ali Morshed holds a PhD in corrosion engineering from University College London, an MSc in corrosion engineering from Imperial College London, and a DIC and CEng. He is the author of five corrosion management books and one MIC book with NACE/AMPP between 2012 and 2022. Ali is a corrosion engineer with more than 21 years of experience and started his professional career in the oil and gas industry back in 2002. Since the introduction of the Morshed Corrosion Management Model (MCMM) in 2012, he gradually expanded his work to many other industries. Ali has worked in the North Sea, North Africa, the Persian Gulf Region, and South Asia. He provides corrosion management and MIC consultancy and training services for various industries.
Background
MIC remains a major integrity threat and a common cause of failure for many upstream, midstream and downstream assets – in spite of the significant technological advances in the areas of oilfield microbiology, metallurgy and used chemicals.
Extensive field experience from both the UK’s North Sea sector and the Persian Gulf region indicates that the main root cause of the encountered MIC cases has been either the total lack of, or inadequate, knowledge and expertise in relation to bacteria and MIC fundamentals among the pertinent personnel. Simultaneously, it has also been observed that oil and gas assets which successfully managed the MIC integrity threat were the ones whose relevant personnel (particularly those managing operations and turnarounds’) possessed adequate competency, mainly through the MIC training they had received.
While MIC incompetency remains the main root cause of a number of highly expensive failures, timely, practical and adequate MIC training is regarded as the key for tackling the spiralling MIC incidents for the oil and gas and other industries assets.
What is MIC?
MIC can be defined as corrosion influenced by the presence, or activity, of micro-organisms [1]. Micro-organisms can cause corrosion problems for various oil and gas assets by their metabolic activities. The corrosion damage inflicted by microbes can be considered “direct” when they create or further increase the environment’s corrosivity (e.g., acid production through their metabolism). The damage is considered “indirect” when they negate a corrosion control measure already in place, thus further promoting corrosion. Such affected corrosion control measures include surface coatings and some dosed chemicals, such as certain types of oxygen scavengers.
A section of failed in-service sea water piping with evidence of metal loss along the bottom of the piping, between the 5 and 7 o’clock positions, is shown in Photo 1. The morphology of pitting suggested that MIC was the cause of the failure. Later laboratory analysis of the corrosion product and biofilm taken from the failed piping section confirmed that the main cause of failure were the sulphate-reducing bacteria (SRB).
Micro-organisms are divided into different groups, of which bacteria are the most encountered in the oil and gas industry. Bacteria are further divided into various categories or families, and sulphate-reducing bacteria (SRB), remain the most predominant and insidious type.
MIC rates, provided that suitable growth conditions exist for bacteria, can be localised and up to several millimetres per year, which is quite severe compared to other corrosion mechanisms often encountered in the oil and gas industry. Corrosion rates have proven hard to predict accurately by modelling. Locations or systems most susceptible to MIC include, but are not limited to:
- Sea water injection
- • Fire water
- Drains
- Stagnant zones such as a by-pass
- Cooling water
- Sand wash water (where treated sea water is used to wash the sand accumulated in various pressure vessels)
- Water displacement systems (where treated sea water is used to empty a product storage tank)
• Wet product transfer pipelines
• Wet product storage tanks
The important caveat regarding MIC is that prevention is always less expensive than cure, because microbial control, once lost, may take years to restore, if at all!
The MIC Mitigation Process
Bacteria and associated MIC mitigation process as depicted in Figure 1 refers to a cyclic—and continuous—process composed of three stages [2]:
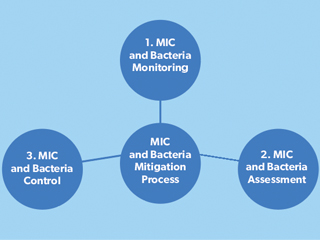
-
MIC bacteria monitoring stage—The necessary sampling (both liquid and biofilm [sessile]) is carried out along the pertaining inspections and corrosion rate monitoring activities (in order to produce the required input data for the assessment stage).
-
MIC bacteria assessment stage—The input data produced in the first stage are evaluated, trended, processed, analysed, and interpreted to determine bacteria types, density, and the concentration of various compounds consumed or produced by bacteria. The input data are also used to estimate or calculate the associated MIC risk although it should be noted that the presence of high bacterial numbers, does not alone confirm that MIC will occur. The microbial investigation is only one aspect of MIC identification and risk assessment.
-
MIC bacteria control stage—In this stage, various activities are carried out to reduce the existing bacteria populations and to decrease the associated MIC risk.
In other words, the MIC bacteria mitigation process consists of three stages, and each stage is composed of two components, one component pertaining to bacteria and the other to MIC. Table 1 provides the associated description and justification for each of the pertaining components.
Stage |
Components |
Justification |
Stage 1:
MIC and Bacteria Monitoring |
Bacteria
Monitoring |
To produce both liquid and biofilm
(sessile) samples for the next stage
(assessment stage). |
MIC Monitoring |
To produce predominantly wall thickness inspection and corrosion rate monitoring data for the next stage (assessment stage). |
Stage 2:
MIC and Bacteria Assessment |
Bacteria Assessment |
To determine types (i.e., metabolism) and density of the bacteria encountered in the system, along with the concentration of compounds consumed and produced by the bacteria. |
MIC Assessment |
To determine whether or not the encountered wall losses or corrosion rates are due to bacteria activities, and also to help estimate the encountered MIC risks. |
Stage 3:
MIC and Bacteria Control |
Bacteria Control |
To use methods to either kill bacteria or retard their activity. |
MIC
Control |
To use methods to reduce or totally arrest the encountered corrosion rates due to bacteria activities. |
Why MIC Still Remains a Predominant Cause of Failure?
Extensive field experience from the North Sea’s UK sector and the Persian Gulf region has demonstrated that the majority of the observed or studied MIC cases were caused by poor, erroneous, impractical, or late decisions and activities associated with the existing bacteria and MIC. Some of such erroneous decisions and activities included:
- Selecting sampling locations where no water was present
- Not capping or sealing the filled sample bottles
- No chlorination at the sea water inlet
- Intermittent chlorination at the sea water inlet
-
Increasing chlorination injection rate significantly to kill sessile bacteria and remove biofilms
-
Using biocide chemicals only effective against planktonic bacteria but incapable of killing sessile bacteria
-
Not coordinating sampling activities with biocide treatments (hence, not being able to determine biocide effectiveness)
- Injecting biocide upstream of the oxygen scavenger injection point
-
Using chemicals which act as nourishment for the exiting bacteria groups
However, the “masterpiece” MIC case belongs to a seawater treatment site that stopped biocide injections for two years. Such a decision induced numerous MIC leaks with an associated repair and replacement cost of more than 100 million US Dollars, just for the first year! Their justification for doing so was that because bacteria are too tiny to be seen by the naked eye, the integrity threat they posed was accordingly negligible; hence, there was no need for any MIC mitigation treatment!
MIC Incompetency Under Closer Scrutiny
The above examples clearly demonstrate that the lack of or inadequate knowledge and expertise in regard to bacteria activities and MIC fundamentals has been the root cause of the majority, if not all, of the observed MIC cases across many oil and gas assets. More precisely, MIC incompetency has been the main culprit behind the encountered leaks and failures. In general, the observed MIC incompetency can be divided into the following four subject areas:
- Bacteria nourishment and growth conditions
- MIC and bacteria monitoring
- MIC and bacteria assessment
- MIC and bacteria assessment
The last three items, when are incorporated with each other comprise the overall bacteria and MIC mitigation process, as was mentioned earlier. Therefore, any shortcomings in properly carrying out any single one of them, could adversely affect the overall bacteria and MIC mitigation process, leading to more problems.
Conclusions
-
MIC remains to be one of the most prevalent and insidious corrosion mechanisms affecting many oil and gas assets.
-
MIC management incompetency has been the main culprit behind
the observed MIC leaks and failures.
Recommendations
-
Timely, proper and practical bacteria and MIC training is crucial for the pertinent personnel and managers, both in engineering and operations.
References
- Standard Test Method: Field Monitoring of Bacterial Growth in Oil and Gas Systems, TM0194-2014, NACE International, 2014, ISBN 1-57590-192-7
2. A. Morshed, A Practical Guide to MIC Management in the Upstream Oil and Gas Sector, AMPP, 2023, ISBN 978-1-57590-424-5.
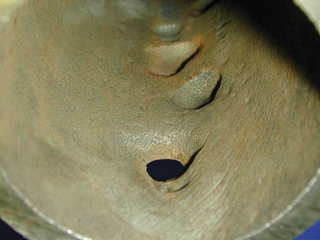
Photo.1: Failed Sea Water Piping Due to MIC, as Indicated by the Severe Pitting Corrosion at the Bottom Line and Later Lab Analysis.
Figure 1: Bacterial and MIC Mitigation Process and Its Three Stages [2].
Table 1- The Components Associated with Each Stage of the MIC and Bacteria Mitigation Process and Their Associated Justifications [2].
Table 1- The Components Associated with Each Stage of the MIC and Bacteria Mitigation Process and Their Associated Justifications [2].