The cart is empty!
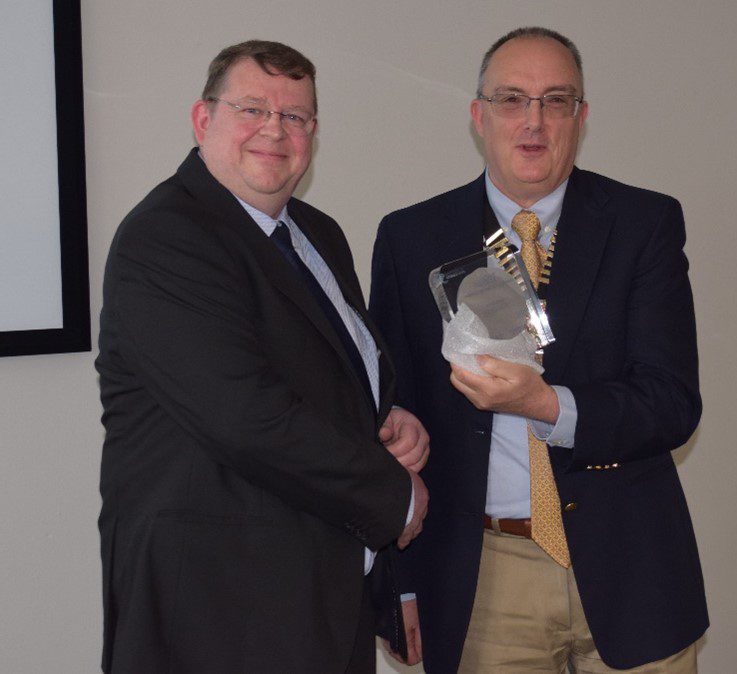
Chris Lynch: Worthy Recipient of the Paul McIntyre Award 2022
Giving Back in Corrosion Engineering
First awarded in 2017, the Paul McIntyre Award is our premier award in the field of corrosion engineering. It is presented to a senior corrosion engineer by the President of the Institute of Corrosion at the Corrosion Engineering Division’s Working Day and Symposium.
In addition to the recipient being a senior engineer, the criteria includes that he or she is a leading practitioner in his or her field who has advanced European collaboration and the development of international standards.
This year, we returned to an in-person Working Day held at the National Railway Museum in York. It certainly proved to be a Working Day and Symposium to Remember, especially for Chris Lynch, who received the Paul McIntyre Award at the end of the morning’s session.
Paul McIntyre – an inspiration to those who follow
Dr Paul McIntyre was determined, invariably polite and accommodating, and had an endearing, dry sense of humour. His career spanned industry, asset management, and editorial work, as well as working on standardisation within the industry.
After graduating from the University of Newcastle-upon-Tyne, Paul spent the initial stages of his career in industry. He moved south in 1978, to join the Central Electricity Research Laboratories in Leatherhead. As Group Leader, he spearheaded studies into stress corrosion, localised corrosion, and corrosion fatigue in conventional and nuclear power plants.
Later in his career, Paul became involved in asset management and remaining life assessment of components, including the development of remedial methodologies such as reliability, availability, and maintenance (RAM) and reliability centred maintenance (RCM).
Between 1996 and 2006, he was the editor of the British Corrosion Journal, though editorial work was not his only foray into the written word in the corrosion industry. Paul authored around 60 published papers and over 200 technical reports.
Paul was never one to rest on his laurels, and thrived on demanding work. If he wasn’t at work, he was deliberating, or brainstorming, or advising. Between 2004 and 2010, he worked as consultant in the Electrochemistry and Corrosion group at NPL. He put his insight and engineering experience to work in producing critical analysis of a wide range of failure investigations including fracture of wind turbine bolts and corrosion pitting in desalination plants, as well as providing informed corrosion control guidance to industry.
Paul also had nearly 30 years of participation in corrosion standardisation as a member of BSI and ISO committees. This included time served as Chair of ISO/NFE 8 Corrosion of metals and alloys, and UK representative on the equivalent ISO committee TC 156 and within that being secretary of WG 2 Stress Corrosion Cracking and member of WG 7 Accelerated Corrosion Tests.
He made an immense contribution as Scientific Secretary of the EFC.
He was also on the Council of the Institute of Corrosion from the early 2000s, specialising in standards work and pan-European activities.
In 2003 Paul was awarded the T. B. Marsden Prize of IOM3 for his considerable achievements in promoting standards, education, and publishing in corrosion and materials. In citation for the award, the Chair of ISO TC 156 said, “Paul has provided more input into the development of ISO standards in the corrosion field than any other individual”.
Unfortunately, Paul was diagnosed with secondary liver cancer in 2012, and, despite his spirit and fight, he sadly passed away in 2012.
The Paul McIntyre Award is a befitting celebration in his memory, and an inspiration to all those who follow him.
Chris Lynch
Chris Lynch graduated from the University of Leeds in 1990.
He began his working career as a junior corrosion engineer at Aberdeen Corrosion Engineers Limited, and remained in the north of Scotland for more than 10 years. Extensive travel took him into Europe and the Middle East, while working onshore and offshore.
Employed by Corrpro Companies Europe Limited in 2005, he is now Senior Engineering Manager and responsible for cathodic protection engineering, site services, and the power unit design personnel.
Like Paul McIntyre, Chris is dedicated to his work and an avid learner. He also believes it is important to give back to the industry he loves and that has rewarded him well.
Also like Paul McIntyre, Chris has served on many committees and with industry bodies. He is Chair of a BSI committee, and has presented training and development courses. He has an international outlook, and thrives on exchange of information with his peers from around the globe. A Chartered Engineer, his rollcall includes:
- Working on numerous training committees
- Course presenter of ICorr training schemes
- Currently a member of the Cathodic Protection Governing Body (CPGB)
- Level 4 CP Specialist of buried and marine structures and internal surfaces
- Fellow of the Institute of Corrosion
- Chair of GEL/603 which is the British Standards Institute (BSI) committee for Cathodic Protection
- Works on various Working Group activities for ISO and CEN
- Member of CEOCOR
- Member of the Marine Corrosion Forum
In accepting the Paul McIntyre Award, Chris said:
“I would like to thank those who have voted for me to receive the Paul McIntyre Award for 2022. This is a great honour for me.
“I would like to dedicate it to all the people who have contributed to my success, many of whom I have met whilst doing the work that Paul himself did tirelessly and for so many years himself.
“It is wonderful that my work with GEL/603 and with ISO and CEN standards committees and working groups has been recognised with this award. The work is so varied and with communities such as CEOCOR, the approach is unique and informal.
“To be honest, it is not work at all. It is fun.
“There is much to be gained in international standards work and I have built up friendships with peers and experts across Europe and the wider world. I have gained so much more than can be taught on courses or read in presentations, papers, or visiting exhibitions.
“I believe we all have something to share. Perhaps an experience we have had that is unique or a set of interesting data we have gathered; or a job that went wrong that others would benefit from in hindsight.”
The similarities between Dr Paul McIntyre and Chris Lynch are uncanny. A worthy recipient of our most prestigious corrosion engineering award.
To learn more about the Institute of Corrosion Awards, click here.
To discover how you can become a member of the Institute of Corrosion, and ways in which membership can help develop your career, or how you can give back to the industry by sharing your knowledge and experience with those who are developing theirs, please contact us.