The branch held its last technical meeting of the 2020/2021 session on 25th May with guest speakers Sieger Terpstra (Shell Global) and Chetan Laddha (Sinclair Energy Partners). This most interesting 2-part talk was entitled: ‘Passive magnetometry based corrosion monitoring and mechanistic simulation.’
In corrosion monitoring there are a number of NDT techniques both automated and non-automated which can be used to detect and monitor integrity anomalies, but these techniques have limitations for remote areas like ‘normally unmanned Oil and Gas platforms (NUI’s) and for locations requiring rope access teams (RAT’s). Additionally, they all require power to be provided for active probes / magnets and to enable wireless operation / data transfer. The Shell Global WiSense project which has been under development for many years, solves most of these issues as it can run on batteries for a 5-year time span and eliminates the need for routine NDT Inspector access, which is a great benefit in hazardous areas. It also eliminates human error in NDT measurement. The WiSense project uses passive magnetometry, a measurement principle that allows monitoring of localised and non-aged based degradation mechanisms, which pose a higher threat than uniform wall loss mechanisms. The passive magnetometry based corrosion monitoring technology has been developed to facilitate area coverage at the target CML’s (corrosion monitoring locations) and provides continuous automated monitoring. Another major advantage is that the sensors do not require any contact with the metal surface – allowing placement on top of coatings or thin insulation and providing frequent, repeatable measurements for trend detection.
When pipes are manufactured they become magnetised and this residual magnetisation can be utilised for fault detection. Defects or ‘missing metal’ with well-defined geometry create detectable magnetic fields inside and outside the pipe. WiSense is a Non-Intrusive flexible patch containing arrays of 3 axis magnetometers sitting on the outer side of the pipe. The magnetometers sense the pipes’ residual magnetic field, and time series subtraction differentiates defect fields from the common pipe baseline magnetic field. The sensor array within the mounted patch produces B-field ‘maps’ resembling dipole patterns and the built-in algorithms find corroded regions by searching for these dipole patterns. The WiSense patch can be deployed in a number of different pipework configurations including straight and elbow sections,
reducer /diffusers, injection points, valves and orifices. The installations from area locations can be monitored on a wireless network through an access point to the control room gateway and a data collection station.
In order to identify defect types, templates are set up by recreating typical defects on pipes using Teflon masking and acid etching of the surfaces to create different types of defects that can then be scanned by the system and used as a model to identify the real and naturally created defects on the pipe. This has been performed on straight and elbow bent pipes both inside and outside. Validation testing can be performed by acid etching on the inside of the pipe while the sensor is on the outside of the pipe monitoring the defect being created. As the magnetometers are detecting dipoles, which are essentially point sources, it is important that real defect geometry is included in the models as they have lateral dimensions and depth, and it leads to a better match than a pure dipole. The technology has been piloted for over 3 years at multiple facilities in downstream as well as upstream areas of Shell operations. Additionally, the technology has gone through independent validation testing with TWI to verify its performance.
In the second part of the talk, the practical benefits of the WiSense technology were further described in relation to commonly applied chemical treatments for corrosion prevention. A mechanistic model was developed to simulate the performance of corrosion inhibition and thereby prediction of inhibited corrosion rates. The overall impact and benefits from corrosion monitoring technology can be significantly enhanced if they are used in parallel with a prediction or simulation technology. The root cause of the majority of Loss of Primary Containment (LoPC) incidents or accidents can often be traced back to degradation mechanisms.
The main driver behind this project development has been that corrosion inhibitors are provided as a “black-box” from the suppliers (exact formulations being closely guarded secrets), which makes it extremely difficult to model the performance of corrosion inhibitors. Additional electrochemical modelling allows testing and simulation of the piping process inhibition mechanisms, without needing to know the underling chemistry of the inhibitor chemical. The simulation can be used to identify both over and under inhibited systems and further, to reduce the cost (corrosion inhibitor qualification programmes. The corrosion monitoring and prediction technologies are used as two complementary tools. Using each tool on a standalone basis has limited value and applicability, however integrating prediction with a real-time feedback loop from sensing allows a step-change in integrity management capability. The combined technologies can help with generating early warnings of integrity issues and facilitate the transition to predictive operation and maintenance.
Upcoming Events:
The branch has several significant events scheduled for later in the summer, including its Annual Corrosion Forum (ACF) on 24th August. This year the event will be held at the TRAC Oil and Gas premises close to Aberdeen Airport. This will be the first branch event in more than a year to be held in person. The theme for the ACF this year is external corrosion management. The programme consists of 8 presentations from speakers from various companies, all very active in the integrity management field. Practical demonstrations in the TRAC workshops will follow in the afternoon. Those interested in joining this event should register their interest with the branch events co-ordinator, Amir Attarchi (amirattarchi@gmail.com), giving full name, company and contact email address
The branch is also supporting the Institute’s ‘Fundamentals of Corrosion for Engineers (FOCE)’ course, which is to be held between 13th – 17th September at the Aberdeen City Jurys Inn Hotel. This course is designed to provide non-corrosion specialists with insights into the principles of corrosion processes and causes which are specific to a range of common industries including: concrete, coatings, cathodic protection, oil and gas, water and renewables sectors. This an intensive one week, classroom-based course with an examination
on the final day.
Applicants will gain a basic understanding of underlying corrosion processes in a wide range of industries which may offer career growth to an engineer, or to anyone who wants to investigate potential job opportunities in corrosion or related fields. On successfully passing the course exam allows personnel with relatively limited work experience in corrosion to apply for Professional Membership of the Institute of Corrosion. Those wishing to attend should download the Application Form from the ICorr Website and submit to: admin@icorr.org. Other general enquiries should be addressed to the Course Leader Dr Jane Lomas on jane7lomas@gmail.com
The branch will also be inviting applications soon for the ICorr Young Engineer Programme (YEP) which it is very pleased to support, following in the footsteps of the highly successful and extremely popular London Branch programmes. For the Aberdeen rotation, the YEP course will reflect the extensive locally based Oil and Gas related Industries and of course also the rapidly growing Renewables Energy Sector. Initial enquiries may be sent to Hooman Takhtechian HTakhtechian@oceaneering.com
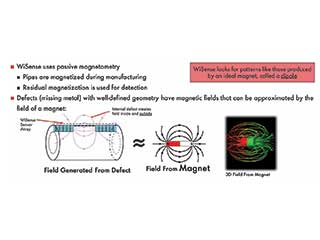
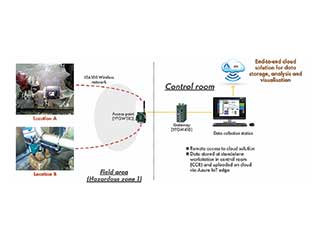