The cart is empty!
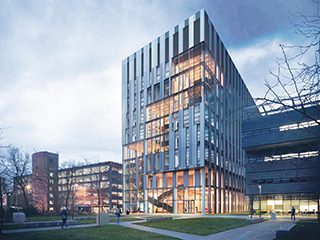
Henry Royce Institute calls for Technology Roadmap
The Henry Royce Institute for Advanced Materials has called for co-ordinated action to address the significant degradation challenges presented by the transition to net zero through a ‘Technology Roadmap for Net Zero’. Such a roadmap would select which technologies should be prioritised for investment and also be attached to key dates linked to when they’re expected to come online. It could also define the most cost-effective investment pathway to net zero, allowing industry and academia to develop Research, Development and Innovation (RD&I) programmes in alignment with clear timescales for delivery.
For many sustainable and low carbon technologies, the degradation of structural materials presents significant and ongoing challenges which can limit the performance, operational life, and sustainability of assets. For example, the financial impact of corrosion, which represents just one of the mechanisms under the umbrella term of degradation, has been estimated at 3.4% of the world’s GDP, thus significant savings could be achieved through better understanding and effective management of materials degradation.
To explore these issues in more depth, Royce commissioned a major landscaping exercise which examined the impact of degradation on wind power generation, carbon capture use and storage (CCS), nuclear fission power generation, transportation technologies (air, road, rail and sea), and hydrogen production and usage, with the overall aim of identifying the materials-related issues affecting the lifetime of structural components, and prioritise the research needed to improve the lifetime of these components.
The report identified a need for high-level strategic direction to guide R&D efforts towards these degradation challenges, but stated that in order for such a strategy to have authority and credibility, it is imperative that it should be developed as a collaborative effort between senior policymakers, along with a broad range of cross-sectoral academic and industrial stakeholders. Bill Hedges, ICorr President, and project champion for the Royce landscape study said: “Significant savings and societal benefits can be achieved through better understanding and effective management of degradation issues. Yet at the moment funding calls continue to encourage an isolated approach to investigating degradation mechanisms and this report recommends that only with a significant change in leadership and policy will the obvious opportunities for transformational change be grasped and ultimately realised. While the report confirms that there were no ‘show-stopping’ issues associated with materials degradation that will block the path to net zero, there are however many opportunities to reduce the costs associated with this.”
As a consequence of this study, the research, development and innovation programmes required to support net zero and tackle the degradation challenge, need to be a collaboration between governing bodies, UK Research and Innovation, major industry players, the supply chain, the Department for Business, Energy and Industrial Strategy, and academia.
The full report can be found at, https://www.royce.ac.uk/collaborate/roadmapping-landscaping/degradation/
For further information, contact Dr Andrew Bowfield, Business Development Manager, Henry Royce Institute, E: andrew.bowfield@manchester.ac.uk, and the report can be found at, https://www.royce.ac.uk/collaborate/roadmapping-landscaping/degradation/
Editor’s Note : The Henry Royce Institute is the UK national institute for advanced materials research and innovation, with the aim of growing, and supporting, world-wide recognition of the excellence of UK materials research, accelerating commercial exploitation and delivering positive economic and societal impact for the UK. With its base in Manchester, it is funded by the Engineering & Physical Sciences Research Council, part of UK Research & Innovation.