The cart is empty!
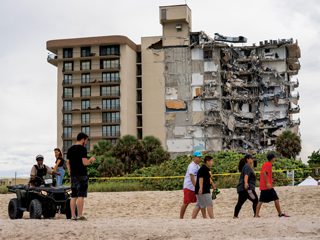
Fellow’s Corner – Issue 165
This series articles is intended to highlight industry wide engineering experiences, practical opinions and guidance, to provide an improved awareness for the wider public, and focused advice to practicing technologists. The series is prepared by ICorr Fellows who have made significant contributions to the field of corrosion management. This month’s contributions include, Bijan Kermani on the problems associated with geothermal energy production, Dirk L. van Oostendorp on challenges of dealing with aging infrastructure, and Dr Gareth John on the multi-discipline nature of corrosion engineering.
Materials for geothermal wells
Anthropogenic global warming (environmental pollution originating from human activity) is the central issue of our time. Shifting weather patterns and the associated consequences threaten the biosphere and human civilisation alike. Global concern about this existential threat/risk has initiated a new Energy Transition (ET). The term is not novel, and incorporates many factors. It has previously been driven by technology, economics, environmental considerations and in developing nations’ living standards. In its current guise, it is also determined by politics, government policy and concerted activism.
Energy demand supplied by hydrocarbons will continue to influence geopolitics in the post-coronavirus world. In the coming years, CO2 and greenhouse gas (GHG) policies will bring continuing changes in how energy is produced, transported and consumed. ET is global, but nations will respond to it differently depending on their own particular circumstances. In this transition, geothermal energy can play a significant role as a source of carbon free and sustainable energy. It can potentially provide a continuous, uninterrupted supply of heat or electricity and become a major contributor to the energy mix to meet a current and future growing global demand.
Geothermal Energy
Broadly speaking, geothermal energy is the natural heat present within the earth’s core, mantle and crust. Typically, this can be divided into low and high energy systems (HES). The former includes direct geothermal applications to heat single buildings, as well as whole districts, and HES covers electricity generation. The associated technologies for each system differ and are greatly influenced by pool depth, geographic location as well as regional geology, and governed by temperature and pressure conditions. HES is most prominent in active tectonic zones in many of the regions of the world, and normally requires relatively deep drilling and is the subject of the present overview.
Use of geothermal energy in HES, generally involves producing and injecting wells. In this, steam/fluid is drawn up in producing wells and eventually enters surface facilities to rotate the turbine and generate electricity. The returning water is then injected back into the reservoir via
an injecting well for pressure enhancement. The simple cycle is schematically shown in Figure 1. Recent developments have achieved a number of milestones in HES including drilling deeper and tapping into hotter sources potentially offering more energy than standard boreholes.
The chemical nature of most geothermal fluids poses some severe technical constraints and many challenges in tapping into these resources. The prevailing conditions include the type of geothermal system, the reservoir depth and the operating conditions. Amongst the challenges are corrosion, particularly affecting carbon and low alloy steels (CLASs) as the main and cost effective material of choice, and scaling of wells and heat exchangers. While corrosion and scale prevention can be achieved by injecting inhibitors based on quaternary amines into the fluids, their applicability and effectiveness are limited. Another main challenge is in relation to constraints on capital investment. These underline the significance of materials optimisation to allow for economic systems which are fit-for service.
This brief overview outlines two elements in relation to geothermal well completion including, (i) types of corrosion threat and, (ii) a summary of suitable tubing materials and their respective optimisation. It is certainly not exhaustive and only attempts to set the scene for furthering future more focussed studies.
Potential Types of Corrosion Threat in Geothermal Wells
Corrosion challenges in geothermal energy production differ greatly from those of the oil industry and may be somewhat similar to those of steam generation, nuclear or the petrochemical industry. Nevertheless, due to the absence of pertinent methodologies, those involved with geothermal well construction continue to adopt oil and gas industry corrosion models and materials selection criteria.
Principal types of corrosion threat experienced in HES include:
H2S, CO2 and low pH corrosion or a combination of these in production mode, and,
Primarily O2 corrosion in the injection mode.
These are to some extent similar to the threats experienced in oil and gas production, such as metal loss or environmental cracking (EC) or a combination thereof. While during production, oxygen may not be present, although it may be involved when using untreated fresh water for drilling, stimulation or in injection mode and subject to well depth. These corrosion threats are particularly in relation to HES, although they may be equally applicable to low energy systems depending on operating conditions.
In addition, erosion-corrosion is also a topic of importance particularly where sediments are lifted with the produced fluids.
The likelihood of corrosion threats for specific well components in the production mode are summarised in Table 1. As mentioned earlier, in the injection mode, unless injection water contains CO2 or H2S, the main corrosion threat is related to the chemistry of injected fluid and the presence of O2 affecting the integrity of fluid flow wetted parts of the well. Where system corrosively is high (red zones), in injection mode O2 corrosion type may take over.
Materials Optimisation
In most high energy geothermal wells (HES), high system corrosivity and low in-situ pH in the production stream renders CLAS unsuitable for fluid flow wetted parts and industry experience of its use has been inconsistent. A summary of materials options for geothermal wells in production mode is presented in Table 2, taking on board both aspects of metal loss corrosion and EC outlining limitations and suitability. This is always complemented with a full reference to whole life costing. It is apparent that for the majority of applications CLAS may prove inadequate in terms of metal loss corrosion resistance, and corrosion resistant alloys (CRAs) including Ti alloys can become the obvious options. In the absence of fluoride species and subject to benign mud acids, Ti alloys in particular have a good track record for such applications. In addition, glass reinforced epoxy (GRE) tubing has been used for low pressure systems at temperatures not exceeding 90 C offering corrosion resistance. In the case of clad pipe, application specific studies need to be carried out.
The case of GRE lined tubing is an ongoing subject, although its use for the injection wells is a proven technology particularly in hydrocarbon producing water injection wells subject to meeting operational conditions. However, minimising O2 entry to the wells can allow the use of CLAS for the injection wells.
Other key points in high energy geothermal well design which require consideration include derating of mechanical properties for tubing/casing grades due to elevated temperature exposure and also potential scaling. However, these are considered beyond the scope of the present article.
While providing an overview, it is apparent that the subject is of great importance and warrants further research in areas of corrosion prediction, materials optimisation and well categorisation to move the sector further forward in offering carbon free and sustainable energy in ET agenda.
Bijan Kermani
Challenges of dealing with aging infrastructures
When we switch on the light at home, it comes on to illuminate the room. When we open the tap, we get water for drinking and cooking. These simple facts are often considered normal in our modern world and taken for granted. However, it is far more complicated than that.
For our electricity, we rely on power generation plants and facilities, and our water is supplied to us through a complex network of purification plants and underground pipelines. The concerning aspect is that the majority of the infrastructure operating quietly in the background is over 40 years old. For most large, cross-country pipelines, they were originally designed for 25 years of service, so we are well beyond that point now, yet still functioning.
Corrosion engineers and specialists are being called upon more frequently to assess the condition of this infrastructure, identify specific areas where remediation is needed, and assist in the process of extending the operating life of these already aged assets. This is a very different role than where corrosion engineers were typically involved in the past, and a different mindset is required when considering an extended timeline.
There have been a fair number of incidents in recent years to remind us of the consequences when aged structures can no longer perform as expected. In-service failures on water transmission and distribution pipelines have demonstrated an increasing trend over the past decade and this represents more of an inconvenience for some people, while it remains unnoticed by the majority of the populace. After all, it is only water, right? Industry statistics indicate that there are approximately 700 water main breaks per day across North America. A study by Utah State University found that break frequency increased by 27% between 2012-2018. Corrosion turns out to be the leading cause of these leaks on cast and ductile iron pipe.
But pipelines are not the only structures that are affected by corrosion, whereby catastrophic failure can occur. The collapse of the Champlain Towers South condominium in Surfside, Florida was a graphic and very visual example. While the investigation is ongoing, it is believed that corrosion on the steel reinforcement was at least a contributing cause.
So how do we properly assess and manage aging assets? For many years, the discussion generally involved the ‘3R’s’ … repair, refurbish, replace. The cost of replacement, coupled with the dependance that has evolved on many of these aged structures, makes replacement very costly and unfeasible. Repair can be a solution for minor damage, or as a short-term measure. This means refurbishment or rehabilitation become the most reasonable approach, meaning we must approach it with different and alternate methodologies.
Over the past decade, there have been tremendous advances made in coatings, composites, and inspection technologies. Using tools like phased-array ultrasonics or pulsed eddy current, technicians are able to look deeper and with more detail into the condition of structures, be it reinforced concrete or pressure vessels. The successful addition of carbon monofibers and Kevlar into composite systems have increased the strength of the final repair, on an antiquated wooden penstock, for example. New epoxy coating formulations have been developed and tested, these include the addition of performance enhancers, such as sintered ceramics, to increase strength and abrasion resistance. Finally, developments in microelectronics have now added the possibility of installing remote monitoring as part of a refurbishment project that allows for real-time assessment of key parameters, such as corrosion rate, cathodic protection potentials or pH of operating environment. With this data, it is possible to apply predictive analytics and determine not only what is required, but also when the necessary work is best completed. In parallel, corrosion engineers are being asked to assess the economic implications of the repairs through Life-Cycle Cost Analysis, as a means to compare the benefits from various repair alternatives and ‘net present value’ considerations of the subject assets.
The role of a corrosion engineer is changing, as corrosion control becomes a more integral part of the overall asset integrity management process, and training in these “new” disciplines is an important part of a corrosion engineer’s professional development. The addition of non-technical skills, such as engineering economics, are becoming important tools for corrosion engineers.
Dirk L. van Oostendorp,
Director of Engineering, Corrpro Companies
The Multi-Discipline Nature of Corrosion Engineering
One of the more interesting aspects I have observed in more than 40 years working in this industry is the frequent requirement to seek input and support from a wide range of scientific / technical disciplines in solving corrosion engineering problems, both large and small.
Generally, corrosion engineering requires input not only from metallurgists / materials scientists (to some, perhaps, the “traditional” corrosion engineer’s background), but also from chemists, chemical / process engineers, mechanical / structural engineers, microbiologists, mathematicians / statisticians, and others. For the modern corrosion engineer, one’s work
can also cross several technical areas, from desktop consulting through to failure investigations, site inspections and audits, as well as laboratory analysis and testing.
In my company (and before that CAPCIS Ltd) I have been privileged to have been actively involved in many hundreds of projects over that time, covering a wide range of industries including oil & gas, petrochemicals & chemicals, water & wastewater, power generation, civil infrastructure, transport, with the work ranging from initial design and selection for new facilities, to operational and maintenance issues and through to failure investigations. In my experience, successful project completion (regardless as to the type of activity) involves input and interaction from a range of specialist disciplines. By way of example, as part of my post-doctoral research project for corrosion of steel in concrete (back in the late 1970’s), I noted that it was only after corrosion scientists and concrete technologists started to talk to each other, with respect to how the chemistry within concrete interacted with the reinforcing steel, was any development / understanding of this world-wide problem developed and, from that, successful solutions for both existing and new structures developed.
It is self-evident that the very nature of corrosion requires a knowledge of chemistry, to ensure an understanding of the electrochemical processes at play and the corrosivity of the environment under investigation. But also, whilst chemical knowledge is critical with respect to assessing if conditions exist for corrosion to occur, the way any material reacts to a given environment also affects how corrosion manifests (if at all); hence, a metallurgical / materials engineering knowledge is also required.
The requirement for input from other technical disciplines varies on a case-by-case basis. For example, input may be required from microbiologists to assess the threat of Microbiologically Influenced Corrosion. Advice from production chemists may also be needed, for example, to perform mineral scale precipitation threat assessments, as well as wax and asphaltene modelling / testing.
In many cases chemical / process engineering input is necessary to fully characterise the extent of corrosion threats across a facility, for example, through analysis of heat and mass balance data, and understanding fluid flow behaviour in a system and consequent impact on water hold-up / drop-out and production chemical performance.
Of course, just understanding the likelihood of corrosion and how it manifests itself is only part of the overall problem, the key question is often “is the structure / component / facility, fit-for-service (FFS)?” This is where mechanical / structural engineering comes in, from simply determining the minimum allowable wall thickness for the item, to determining the limiting conditions for corrosion damage. For example, determining critical defect size for the operating pressure (or the inverse, the safe working pressure for an existing defect), to critical defect size for crack initiation / propagation and overall fatigue life.
Finally, mathematics in general (and statistics in particular) play a key (if often overlooked) role in day-to-day corrosion engineering. Many corrosion-prediction models (as well as integrity models) are statistical in nature as they provide an estimation of the corrosion rate / failure condition under different conditions by interpolation and extrapolation of results from laboratory tests and (in some cases) real life data. Data trending to allow extrapolation from current to future conditions is also a major aspect of corrosion engineering. Fundamental to any such analysis is a need to understand that any model is based on assumptions and/or a limited data set, and hence, having the knowledge to understand when to accept and when to question the results is also vital.
A good example of a multi-faceted project is one we carried out for ADNOC Offshore (then ADMA-OPCO) several years ago in relation to assessing the impact of a proposed CO2 enhanced oil recovery (EOR) project for a mature offshore field [1]. In this case there were significant concerns given the assets were over 40 years old and several subsea flow lines and other facilities would be directly impacted. At the time there was very little published information relating to expected corrosion in the various operating conditions that would be created by the new CO2 EOR and most predictive models had not been verified for the very high partial pressure of CO2 that would be encountered.
As such, the study covered a wide range of interrelated tasks including:
• Process engineering – to assess issues associated with handling super-critical / dense phase CO2, including predicted varying process compositions / production rates for the different field assets / facilities.
• Corrosion modelling – to estimate expected corrosion rates for the range of operating conditions covering varying partial pressure of CO2 / H2S, and water content.
• Laboratory testing – to confirm corrosion rates for natural (non-inhibited) and inhibited conditions, under super-critical CO2 conditions.
• Statistical analysis – to compare the corrosion rates from the modelling work with laboratory test data and hence to provide realistic predicted rates across the facility.
• Integrity assessment – based on the condition of the existing assets / facilities and expected future corrosion rates, perform integrity and remaining life assessments.
• Corrosion monitoring – identifying what system modifications / additional facilities would be required to ensure adequate on-going corrosion monitoring and assessments.
• Field surveys – to assess the existing facilities and have discussions with on-site personnel.
• Materials selection – for the new injection and production wells, including use of corrosion resistant alloys for different components.
• Production chemistry – to determine the expected impact of asphaltene formation (due to changes in system pH from CO2 injection) and options for mitigation.
Considering all the different scientific and engineering aspects that need to be taken into account, it is not surprising that a Corrosion Engineer is often considered as a jack-of-all-trades (although I prefer the more poetic term polymath). However, whilst a broad overall knowledge may be sufficient for routine situations, the above makes it clear (I trust) that for many complex cases it is important that expertise from all the appropriate technical disciplines, and input from different sources, are utilised to ensure that a fully comprehensive and effective solution is developed and applied.
My own background, BSc in Chemistry & Mathematics, followed by a PhD and post-doctoral research at the Corrosion & Protection Centre (University of Manchester) before joining CAPCIS back in 1981, has allowed me to get involved across all the different scientific, technical and engineering areas I have discussed above. I must admit that it is this multi-discipline nature of corrosion, with all the different challenges that it throws up, that makes it such an interesting and intellectually rewarding field to work in.
(1) H A Binthabet et al Corrosion management challenges related to CO2 enhanced oil recovery on existing production infrastructure, paper no 7649, presented at NACE Corrosion 2016, Vancouver, Mar-2016.
Dr Gareth John, Executive Consultant, Intertek Production & Integrity Assurance.