The cart is empty!
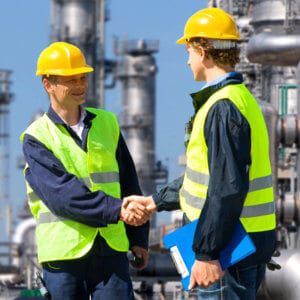
Cathodic Protection Training: The Role of the Cathodic Protection Governing Body in the Institute of Corrosion
Ensuring Industry Leading Training in Cathodic Protection
The Institute of Corrosion’s successful and growing Cathodic Protection Training and Examination Scheme (‘the CP Scheme’) is managed by the Cathodic Protection Governing Body (CPGB) in accordance with BS EN ISO 15257:2017. While not responsible for the assessment and certification processes of the scheme (this is one of the roles of the Professional Assessment Committee – PAC, in order to ensure that the assessment and certification are both independent of the training), the CPGB’s remit is wide-reaching and detailed.
Structure of the CPGB
Appointed by the Institute of Corrosion, the CPGB reports to the Professional Development and Training Committee (PDTC). The CPGB consists of a Chair (appointed by PDTC), a secretary, and at least three others. The maximum number of members is limited to eight, though a member of PAC may be invited as an additional CPGB member from time to time (without voting rights).
At least half of CPGB members must be certified to a minimum of Level 4 (or equivalent) in accordance with BS EN ISO 15257. In addition to this requirement, there is a minimum of one specialist in each of the four sectors of Cathodic protection.
Roles and Responsibilities of CPGB
The primary responsibility of the CPGB is to ensure the success and competence of the ICorr ‘CP Scheme’. This responsibility has many facets:
- Ensuring that the ICorr ‘CP Scheme’) is compatible with the requirements of BS EN ISO 15257 and BS EN ISO/IEC 17024:212 (Conformity assessment – General requirements for bodies operating certification of persons) and remains so regarding all revisions to these two standards.
- Ensuring that the training courses and examinations are rigorously and competently delivered in accordance with the requirements of the ICorr Qualification Procedures Document, including audits of training and examination centres, assessing and approving Tutors, Examiners and Moderators and providing sufficient courses to meet industry requirements
- Reviewing all activities and documentation associated with the Scheme to ensure they are fit for purpose for present CP best practice and standards. This review is completed each year.
- Auditing the syllabi, course content, and course delivery of the Scheme. This includes technical and compliance audits.
- Establishing and auditing the content and process of the examinations under the Scheme
- Advising PAC on the assessment of experience requirements for applicants to meet the requirements of BS EN ISO 15257.
- Ensuring that any technical developments in coatings, corrosion, and cathodic protection are incorporated into the Scheme. This involves suitable liaison and common membership within the relevant BSI, CEN, and ISO committees, thus ensuring that the ICorr ‘CP Scheme’ is kept up to date and that the international standards reflect actual best practice.
- Ensuring that the potential users of the CP Scheme, asset owners onshore and offshore, pipeline, storage and infrastructure owners, specialist CP contractors and consultants along with independent CP personnel are all aware of the need for and benefits of competence training, assessment, and certification. Striving to promote the use of ISO 15257 as the appropriate mechanism for this.
- Delegating day to day activities to the ICorr CP Scheme Manager, receiving and reviewing his or her progress reports on these activities and ensuring that the agreed course and examination programme is smoothly delivered to the satisfaction of candidates with the full rigour of ISO 15257.
The CPGB must ensure it remains impartial, and manages potential conflicts of interest to maintain objectivity in the training, examination, and certification of cathodic protection personnel.
The CPGB may, on occasion, work closely with PAC. This includes collaborating to ensure that training and examination procedures and standards remain in compliance with ISO standards. However, it should be noted that, in accordance with requirements for impartiality and confidentiality, it is the PAC that maintains sole responsibility for certification of cathodic protection personnel.
CPGB is accountable for approving the trainers and training providers who deliver ICorr’s CP training. It also leads in the drafting of agreements between ICorr and the training centre providers for approval by PDTC and Council. Recently CPGB has become responsible for the administration of the new ICorr Dante software-based booking and payment system, jointly with ICorr Trustees and the overall ICorr administration, as these tasks have been brought fully ‘in house’ for the first time.
How the CPGB works
The CPGB meets physically at least once each year, and the following points must be included in the agenda of this meeting:
- Reviewing the Terms of Reference (ToR) and making recommendations for their revision to PDTC.
- Assessing the compliance of the Scheme with the requirements of ISO 15257 and ISO/IEC 17024, and preparing a report of such to the PDTC/Council.
- Summarizing the review and audit actions taken, reporting on whether the requirement for reviews and audits has been met, and presenting the outcomes of the reviews and audits along with any resulting changes.
- Assigning review and audit tasks for the following 12 months to CPGB members and external reviewers and auditors appointed by the CPGB.
- Evaluating the activities of the CPGB regarding specific items and creating a report for PDTC/Council.
- Assessing the activities of CPGB members throughout the year and determining if any replacements are needed.
Between annual meetings, the CPGB conducts much of its activities electronically. This minimizes the need for physical meetings and helps to maintain financial prudence. These meetings address, primarily, the ongoing progress, challenges, and opportunities in respect of the primary responsibilities of the CPGB summarised above.
The secretary is responsible for recording all meetings (physical and electronic discussions) as well as any data exchanges. He or she is also responsible for compiling CPGB annual reports and making them available to the Council of the Institute of Corrosion. If any sensitive items are included in the reports to PDTC, the report to the Council may be edited with agreement from PDTC and CPGB chairs.
The President of ICorr and the Chair of PDTC have the right to attend CPGB meetings and speak on any matter, but not vote.
CPGB members are expected to serve on the CPGB for between three and five years. The Chair’s term is also expected to be 3-5 years.
In summary
The CPGB is closely aligned with various bodies within ICorr, and works closely with BSI Standards committees when necessary. It is the key force in delivering qualification, assessment, and certification for cathodic protection personnel in the UK, as well as ensuring that the quality and value of the ICorr CP Scheme is maintained.
If you would like to know more about the Institute of Corrosion CP Training and Certification Scheme and post-examination assessment for Levels 1, 2, 3, and 4, and Level 5 Assessment please visit our cathodic protection training pages, or email the Institute of Corrosion.