Uncategorized
The branch started the 24/25 season on Thursday October 10th with an in-person presentation by Ali Morshed on “Why is corrosion still a major integrity threat for many industries in the 21st century?” at the usual venue, the Lancaster Hall Hotel, Bayswater.
Ali Morshed holds PhD in corrosion engineering from University College London, MSc in corrosion engineering from Imperial College London, DIC and CEng.
He is the author of five corrosion management books and one MIC book with NACE/AMPP between 2012 and 2022. He is a corrosion engineer with more than 21 years of experience. Ali started his professional career in the oil and gas industry back in 2002, but since the introduction of the Morshed Corrosion Management Model (MCMM) in 2012 he has gradually expanded his work to many other industries.
Ali has worked in North Sea, North Africa, the Persian Gulf Region and South Asia. He provides corrosion management and MIC consultancy and training services for various industries.
A full description of this presentation will be reported in the next issue of Corrosion Management.
Upcoming Events
Readers are reminded of the ICorr 2024 YEP – Final Presentation of Case Studies, to take place on 21st November 2024,
15:30 – 21:00 at: Lancaster Hall Hotel, Craven Terrace, London, W2 3EL hosted by ICorr London Branch.
On December 5th, the branch will host its annual Christmas luncheon at the Royal Overseas League, St James’s, London, where the guest speaker will be Garry Richardson. Gary is a BBC Sports presenter, best known for his witty sports reports and interviews, and an experienced after-dinner speaker. He has presented Radio 4’s prestigious ‘Today‘ programme for
four decades.
For more details about sponsorship of this event or to book tickets, please contact Steve Barke at sjbarke@gmail.com
Photo: Ali Morshed, Independent
Corrosion Engineer.
Uncategorized
Screening Tests for Corrosion Inhibitors
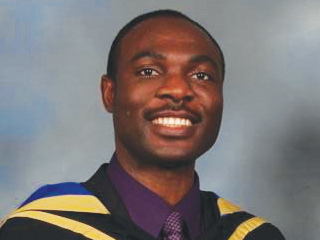
By Joseph Itodo Emmanuel
Meet the Author
Dr. Joseph Itodo Emmanuel
Joseph Itodo Emmanuel is a corrosion specialist with core expertise in corrosion and integrity management in the upstream, mid-stream and downstream sectors of the oil and gas industry.
He is Chartered Engineer registered as a European Engineer with FEANI (Europe),
and also a Fellow with Institute of Corrosion (UK).
Joseph obtained his Bachelors in Chemical Engineering from FUT Minna, Nigeria, Masters in Science (MSc) from Heriot-Watt University, Edinburgh, UK, Masters in Business Administration (MBA) from University of South Wales, UK and Postgraduate Certificate in Education (International) from Liverpool John Moore’s University, Liverpool, UK. He is a certified Corrosion Specialist, Chemical Treatment Specialist and Cathodic Protection Specialist. and also a member of SPE (USA), AMPP USA), EI (UK), IET (UK), COREN (NIG), NSChE (NIG), COREN (NIG) and NSBE (USA).
Joseph is a trainer, scholar, mentor, STEM facilitator, and author of books and peer
reviewed journal publications to his credit.
- How do we best screen for Corrosion Inhibitors?
There has been a growing call by stakeholders in academia, industry, and government for a switch from conventional chemical inhibitors due to their high toxicity and harmful impact on human, environment, and aquatic life to organic green corrosion inhibitors (OGCI) developed from nanomaterials and plant extracts through green synthesis. The preference for OGCI developed from nanomaterials and plant extracts has led to renewed global interest, with a focus on sourcing OGCI materials from plant extracts. OGCI from plant extracts have strong adsorption, eco-friendliness, non-toxicity, non-bioaccumulation, biodegradability, extraction ease, availability, and cost effectiveness.
Laboratory Screening Test for Candidates OGCI
After the initial laboratory static testing of the proposed candidate OGCIs, those with good performance (high efficiencies) above 80% are then subjected to a four-phase test programme. These tests are aimed at ensuring the candidate OGCI meets the stringent industry requirements by functioning with similar efficiencies under field-simulated conditions.
-
The first phase involves the testing of the physical and chemical properties of the candidates OGCI and a robust verification process by assessing the quality assurance and control (QA/QC) parameters.
-
The second phase, involves bubble tests at near-field operating temperatures and pressures to screen the performance of OGCI for field application before field trials. The test temperatures can vary between 37 to 40 oC (this is a very low temperature range v industrial applications), and the test pressure is simulated to be close to the operating pressure of the pipeline to be inhibited and for OGCI to be deployed for sub-surface facilities, higher test bubble pressures and temperatures are technically recommended considering the higher operating temperature downhole and the need to simulate near-field conditions. These tests can be conducted in the brine phase or in a in a crude oil and brine mixture. The bubble test can also be divided into three subsets: the first simulating a sweet corrosion environment using carbon (IV) oxide (CO2), the second simulating a sour conditionusing hydrogen sulphide (H2S), and the third simulating a sweet and sour condition using a mix of carbon (IV) oxide (CO2) and hydrogen sulphide (H2S).
-
The third phase involves conducting a dynamic test using a rotating cylinder electrode (RCE) to replicate (duplicate) the real-field operating pressure, temperature, and flow effects. During this phase, if the candidate inhibitor is tested for gas systems and not oil or water systems, it is also tested for the likelihood of hydrogen-induced cracking (HIC).
-
During the fourth phase, the OGCI candidates are subjected to a supplementary test, viz., a pitting test, to confirm the presence or absence of pitting using test coupons (strip coupons).
Field Trial for Candidates OGCI
After the candidates OGCI have passed the laboratory screening test, they are further subjected to laboratory field trials as a final test to determine OGCI efficiency in the live system and to assess and evaluate secondary effects, viz., compatibility, physical (fouling), and functionality with other oilfield chemicals, process fluids, chemical injection pump parts, and materials (seals, etc.).
The effects of the dosed OGCI further downstream from the injection location include the likelihood of forming emulsions, the secondary effects of oil on the quality of the produced water, the stability of the formed foams, and general effects on people and the environment in the event that the product is accidentally discharged or spilled. In addition, a range of process stream parameters should be considered as they have effects on the corrosivity of the test system, viz., operating pressure, operating temperature, water cut, flow rate (flow regime), CO2, H2S, dissolved oxygen, organic acids, free sulphur, SRB (bacteria), water chemistry, organic acids, scaling tendency, total dissolved acids, pH, and gas oil ratio (GOR) (59, 60). The four most commonly used laboratory methodologies and standards for evaluating corrosion inhibitors in general for oilfield and refinery applications are presented in Table 1 on the next page.
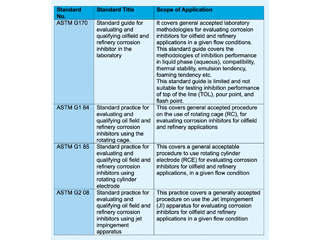
Secondary Effects Associated with Testing OGCI
During the field trial of the screened OGCI, the secondary effects are closely monitored by implementing the required procedures, checks and test protocol to ensure OGCI is compatible with system fluids at recommended injection rate (dose rate), water cuts, other production chemicals (emulsifier, oxygen scavengers, flow assurance chemicals, biocides etc.), storage and pump materials, wetted materials within the system, and process stream. The secondary effects, performance check and test protocol carried out are summarised in Table 2 below.
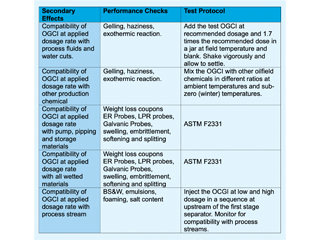
Prospects, and Challenges
Empirical studies have revealed good inhibition efficiency for OGCI developed from nano sized plant extracts and nanomaterials. However, the reported inhibition efficiency from gravity (weight loss) and electrochemical methods would not qualify when subjected to stringent industrial screening tests, viz., kettle (bubble) tests, rotating cylinder electrode (RCE) tests or cylinder electrode rotating cages, jet impingement, high-pressure loop tests, wheel tests, localised corrosion tests, and autoclave tests. To validate the reported performance data, the same product should be tested under industrial conditions. In addition, there is the need for the chemical and physical properties of the developed OGCI to be further investigated under field operating conditions to evaluate their solubility in produced fluid, their emulsion forming tendency, their foaming characteristics, thermal and hydraulic (pressure stability), compatibility, film persistence in in-service conditions, and optimum protection at optimum inhibition efficiency. Also, more studies of OGCI made from nano sized plant material extracts and nanomaterials need to be undertaken to investigate the complex corrosion inhibition mechanism of plants-based extracts on carbon steels and other alloys.
Table 1:Laboratory Methodologies Standards for Evaluating Corrosion Inhibitors.
Table 2: Secondary Effects, Performance Check and Test Protocol.
Uncategorized
On 16th May 2024, the Wales and South-West Regional Branch held an event at the Steel and Metals Institute covering the topic “Hydrogen research capabilities – now and into the future.”
Dr Barrie Goode discussed in detail the requirements for progressing in this important area of research. Barrie is the Director of Industrial Research at the Steel and Metals Institute (SaMI), an ‘open access’ innovation centre, based at Swansea University. With a Doctorate in Engineering, BEng Materials Science and Engineering and over 20 years of experience in the steel and metals industry, Barrie has held senior positions in a number of businesses within the technical and operation functions, including electrical steels. He joined SaMI in 2019 and is responsible for developing and managing relationships with industry and setting the direction for the internal operations to meet customer research demands effectively. He also has an MBA from the University of Warwick and is a chartered engineer and Fellow of the IOM3 (Institute of Materials, Minerals & Mining).

Refer to: www.samiswansea.co.uk and recent blogs at:
www.samiswansea.co.uk/blog/
He is also a valued member of the Wales and South-West committee, its current student and liaison and CPD officer.
The Steel and Metals Institute collaborates with a wide range of partners to develop both public and privately funded research aligned to industry needs, with a focus on decarbonisation and product development. The development and evolution of hydrogen testing capabilities have been at the forefront of the facility’s growth and will continue to be a key focus to support the requirements of industrial stakeholders moving forward.
This most interesting presentation provided an insight into the hydrogen testing capabilities currently on offer at the Institute and the ongoing research and development programmes being