In February, the branch welcomed Dr Mohammad Seyed Hosseini, Technical Director at London Petrotech Engineering Ltd and Principal Consultant at Subsea 7, based in London, who presented “Lessons-Learned from a Root-Cause Failure Analysis Conducted on a Subsea Sour Gas Pipeline.”
Dr Hosseini, is an accomplished materials and corrosion engineer with over 24 years of experience in the oil and gas industry. He has worked with some main EPCI contractors and major operators. In addition to his industry accomplishments, he holds an academic position in the UK, where he has spent years lecturing, researching, and supervising postgraduate students. He has also delivered several training courses to institutions and directly to oil and gas companies.
Dr Hosseini started by describing the subsea pipeline failure. It was transporting wet sour gas and experienced multiple failures within two years of the start of operation. The pipeline, constructed from DNV SAWL (longitudinally welded steel pipe manufactured using the Submerged Arc Welding process) 450 SD material, was thus subjected to a comprehensive three-stage investigation, including laboratory analysis, Root Cause Failure Analysis (RCFA) by the operating company’s expert, and an independent review by a contractor-appointed expert.
He then described the detailed examination conducted through laboratory investigations on the pipes retrieved from the seabed, which revealed several key findings. Visual inspection revealed ruptures in the base metal with extensive internal corrosion concentrated at the 10-2 o’clock position of the pipe sections. Despite chemical composition and mechanical properties (including toughness and hardness) meeting all required specifications, microstructural examination showed banded structures at mid-thickness with elongated inclusions. Ultrasonic testing detected several Hydrogen Induced Cracking (HIC)/Stepwise Cracking (SWC) indications at the mid-thickness, all located at the top of line (TOL). HIC/SWC tests confirmed acceptable results for most samples except one, which was taken from the parent material adjacent to the rupture point.
A holistic root-cause failure analysis was also performed based on BS 62740 using the Cause Tree Method (CTM). The relevant design, manufacturing, construction, installation, pre-commissioning, and operational data were reviewed. The RCA results showed that the primary root causes were material quality issues making the pipeline susceptible to HIC damage, with corrosion processes in wet H2S environments leading to critical hydrogen absorption. Contributing factors included inadequate corrosion control strategies, infrequent pigging operations that allowed liquid accumulation, and higher-than-anticipated H2S concentrations accelerating corrosion. Manufacturing inconsistencies and insufficiently rigorous HIC testing procedures further compromised the pipeline’s integrity.
The independent expert reviewed these findings and highlighted important enhancements needed in Root Cause Analysis methodology. It emphasised that RCA should be holistic and collaborative, with regular inter-stakeholder workshops to discuss interim results. The basis for selection of RCA techniques must be mutually agreed upon by all parties, and a minimum of two complementary techniques should be employed. Incorporating interviews with key personnel and utilising specialised RCA software tools were also recommended to improve investigation quality.
A pivotal conclusion emerged regarding the relationship between TOL corrosion and HIC. The analysis definitively established a sequential relationship where these mechanisms occur in series rather than in parallel. This means that TOL corrosion triggered HIC in the steel, which ultimately led to pipeline structural failure and rupture.
The expert also noted that microstructural imperfections like banding are unavoidable in thermomechanically-controlled processed steels but require careful management. These highlighted the lack of clear requirements in the current industry standards and practices regarding acceptable banding structures for sour service applications. For severe sour service environments, the expert recommended using quenched and tempered (Q+T) or normalised steels where feasible, though acknowledged this approach was not applicable to this pipeline’s large SAWL pipes. Dr Hosseini concluded by noting that these comprehensive findings provide critical insights for preventing similar failures in sour service subsea pipelines through improved material selection, manufacturing quality control, and corrosion management strategies.
The branch held their AGM on Thursday, 13th March. The chair summarised the past year and highlighted the upcoming events. The treasurer, Jim Glynn, presented the accounts, which showed we were able to run all the events and still return some of our allocated funds to Head Office. Acceptance of the accounts
was proposed, seconded and approved. There were some changes to the committee; Ali Morshed resigned due
to family commitments, Alejandra Fernandez-Vinas was going
on maternity leave, and we had one new member, Berenika Syrek-Gerstenkorn. This new committee was elected for the 2025-2026 season.
Following the AGM, the chair gave a very interesting talk on “Work-Life balance”, he explained that after (potentially stressful) work, it is necessary to have another relaxing interest, e.g. a hobby, and in Paul’s case, it is bee keeping.
He explained the function of a colony of bees in a hive. Honeybees play a crucial role in pollinating crops and plants, ensuring the production of many of our fruits, etc. They produce beeswax which they use to build their hive. Going from autumn to winter, a hive has about 6-7,000 bees (worker bees and the queen) – during winter they are dormant and mainly generate heat by vibrating their wings while clustered around the Queen Bee, keeping her warm and fed, consuming the honey stored up during the previous summer.
For a bee hive to be successful, it must have 1,000s of worker bees and one queen bee and drones (male bees). The primary purpose of the Queen in a hive is reproduction, she is the only bee capable of laying eggs, essential for maintaining and expanding the colony , she produces pheromones that help maintain the cohesion and stability of the colony , and is crucial the colony’s survival.
Drone bees are prevalent in colonies in the spring and summer months. As winter approaches, they are driven out of the nests or hives by the worker bees and left to perish in the cold. When a brood nest is large, the presence of drones helps to maintain heat, and it’s believed that a colony is more content with drones.
Worker bees are females which lack the reproductive capacity of a Queen and carry out the majority of tasks needed for the hive to function – they are by far the most numerous types of bee, smaller than drones and Queens, and have bodies specialised for nectar and pollen collection. They perform different tasks around the hive progressively over their lifespans in a predictable order based on their age.
Worker bees gather pollen in the pollen baskets on their back legs and carry it back to the hive to feed the developing brood. Nectar is sucked up through the proboscis, mixed with enzymes in their stomach, and carried back to the hive, where it is stored in wax cells, and evaporates into honey. There are also Guard bees who stand at the front of the hive entrance, defending it from any invaders, such as wasps.
A beehive is analogous with a large company. The Queen is the CEO, the workers carry out all the tasks, and the drones are the seasonal workers, whilst the guards are the security, just as in our industry. There was an interesting discussion about the honey produced and the different flavours that are obtained. As is customary with the branch, the speaker received an ICorr pen as thanks for his talk.
In May, the branch will be holding a social event for members and their partners. Further details will be available on the ICorr website in due course.
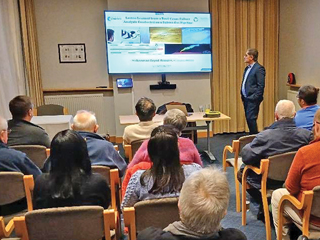
Photo (right)
Dr. Mohammad Seyed Hosseini Delivering
His Talk.
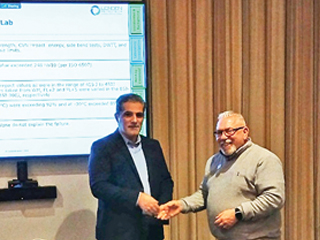
Photo: After a Very Interesting Q&A Session, the Chair Thanked Dr Hosseini for His Presentation, and Presented Him with an ICorr Pen, in Appreciation of His Talk.
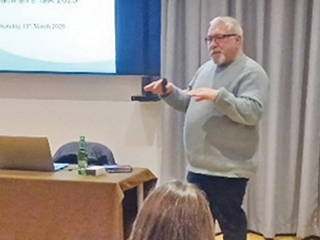
Photo: Paul Brooks Delivering His Talk.
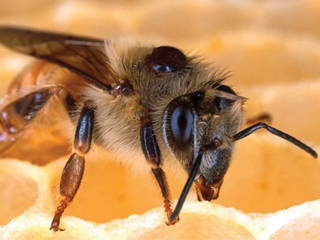
Photo: Honey Bee.