Latest News, North East Branch
The January meeting was joint with TWI, when Neil Gallon & Michael Young of Rosen presented a talk on Preferential Weld Corrosion (PWC).
This was the first of its type in the North East aimed at creating some synergy between ICorr and TWI. A good crowd over 20+ came to hear the presentation which went into in detail about the differences and complexity of welds in pipelines, and the possibility of galvanic corrosion causing the metal adjacent to the weld being consumed. The heat affected zone (HAZ) can be attacked preferentially to the weld because of changes in morphology and differing galvanic potentials. Potential issues are very difficult to diagnose and therefore a lot of work has been done to understand the effect of adding corrosion inhibitors, for example when they are added to water injection/production pipes to protect the base metal, however this can also cause issues as they do not protect the weld. In these cases the weld can become anodic and preferential weld corrosion can occur.
One very interesting question was asked about the potential ‘double whammy’ of PWC and CUI occurring at the same time. It was confirmed that this could potentially occur if the insulation system was damaged allowing water to enter the system and causing electrolytes to leach from the insulation and gather at the weld. In summary the evening was great success and this type of joint meeting will be used again.
This report was inadvertently published under the Midland Branch in the last issue.
Latest News, Midlands Branch
The May meeting was a very interesting presentation on the future of ICorr, by the President, with lots of input and discussions from the branch members. Whilst the meeting was well attended there is always room for more, especially during a presentation by the institute’s President. The role of the Institute in the day to day corporate environment was discussed, with many far reaching improvements being tabled by Gareth.
In September, the branch is hosting a half day event on the Severn Valley Steam Railway, with tours of the engine house and a ride out on a private ICorr carriage, with food and drinks provided. The event is open to all branch sponsoring companies initially as it is being held to thank them for supporting Midlands branch, but tickets will be available to purchase for individuals. This promises to be a great networking event, and more details will be available in
due course.
Latest News, London Branch, Uncategorized
T
he branch AGM was held in March, which was followed by the “President’s talk”. The chairman, Paul Brook, reviewed the activities of the branch over the past year and noted that we had had excellent presentations. The Treasurer, Jim Glynn, announced that again our finances were in good shape, and that surplus monies will be returned to head office. Paul then asked if any members wanted to join the committee, and confirmed that existing members were happy to serve for another year. Paul also informed the meeting that the branch is close to completing a venue move from Imperial College, Kensington to the IMechE offices in Bird Cage Walk, Westminster. This should be a great home for London branch future technical talks, which will restart following the summer recess in October, on the second Thursday of the month as usual. More details will be available on Institute web site in due course.
Gareth Hinds then presented his views on the future of the Institute, and discussed ways we could adapt to changes, including environmental challenges, the rise of digital communications, and how to encourage more young engineers to join the Institute, and how to support them. This generated a lot of discussion and interesting suggestions.
The April meeting, the last of this season, was joint with The Welding Institute, and was given by Alan Denney of TWI, on the subject of “High tensile steel bolts and nuts: hydrogen embrittlement and failure in corrosive environments.’
Alan started by talking about the failure of threaded components used as shear connectors for earthquake resistance on the San Francisco Oakland Bay Bridge, which has been well documented in the technical press in the USA. These galvanised rods (in ASTM A354 grade BD steel) were pre-installed in 2008 in the supporting piers to the bridge superstructure which are above the water level. The superstructure was assembled and in 2013 the rod connectors were pre-tensioned hydraulically to 70% of UTS. A number of these suffered brittle failure, the published cause of which was that the rods failed due to hydrogen embrittlement arising from stress corrosion cracking.
Alan then proceeded to explain the conditions required for stress corrosion cracking, namely a combination of a susceptible material, a source of the hydrogen, and tensile strength above a threshold value. He explained that the hydrogen could be either from internal sources in manufacture, or from an external source. The potential sources in manufacturing include hydrogen retained from steelmaking or hydrogen resulting from pickling of the components prior to coating. The external source would result from corrosion, the hydrogen being generated by the cathodic reaction. He explained that failures can occur in nuts as well as the bolts or threaded rods, and that in galvanized components
the zinc acts as a barrier to the outward diffusion of any trapped hydrogen.
Failures of structural bolts have a long history. Alan mentioned that his first encounter with bolts failing from hydrogen embrittlement was in the 1970s on a television transmission tower, with failures occurring in V grade and Y grade bolts on cold nights; the bolts being found on the ground in the morning, and his most recent experience of a failure was a few weeks before this talk. Apart from in transmission towers, such failures have also occurred in the recent past on prestigious building structures, and in offshore wind turbine towers. Recent occurrences known to Alan have been in large diameter high tensile bolts, generally in bolt grades 10.9 and above. He explained that there was a relationship with hardness of the fasteners (both bolt and nut), and covered recommendations in standards such as those published by DNV-GL for offshore wind turbine structures, which limit the highest strength grade to 10.9. He discussed the typical crack morphologies associated with hydrogen embrittlement and how the fracture surface could be ‘read’.
Alan then discussed some of the metallurgical aspects in bolt and nut materials and the recommendations and findings of work carried out by the Deutscher Schraubenverband (DSV) in relation to the desirable elements in the composition, and their proposed limits on chemical composition. He presented some findings from DSV on the failure thresholds in 10.9 bolts under ASTM F1624 test conditions with different coating types and then finished by summarising the findings:
n There is a risk of stress corrosion cracking with the use of fasteners with a UTS > 1000 N/mm2 in a corrosive or marine environment.
n The much-quoted guideline of 380 Hv as the threshold for stress corrosion cracking is not conservative, notably when there is a risk of external corrosion, even during temporary conditions.
n Controls which will improve their performance in marginal situations can be put in place for the bolt materials, their heat treatment and metallurgical controls, their coating systems and application, and their quality control and testing requirements .
However the main means of avoidance of SCC is to control the environment.
There was a lively question and answer session, with interesting contributions from the audience and the meeting was closed with a vote of thanks and a presentation to
the speaker.
Aberdeen Branch, Latest News
The March meeting was an industrial event at ICR, Bridge of Don, with group presentations and demonstrations of three of ICR’s core business activities.
ICR have specialised tooling and trained engineers, who deal with the insertion and retrieval of corrosion monitoring coupons in live pipeline valve stations (Online Retrievals).
Pre-installed fittings on the pipes allow threaded plugs which carry the mounted coupons to be inserted into the pipe.
This is carried out using either mechanical or hydraulic, telescopic portable tooling which can introduce, through the valve gate, fresh coupons of prepared carbon steel which then sit within the line for the study period. Recovery of the coupons allows for weight loss assessment and corrosion pattern studies, which can be used to evaluate the corrosive nature of the fluid and help to provide remedial measures, such as chemical injection solutions.
ICR also offers on-site weldless, flange to pipe connections which are carried out using a hydraulic colleted + ram system. The flanges to be fitted to the pipe have an annular groove in the inside into which the wall of the pipe can be expanded using tooling inserted inside the pipe end. The hydraulic ram contains a split collet which expands inside the pipe and forces a ring of the pipe wall into the flange grove. This provides a weldless metal to metal gas tight seal which is dressed each end with sealant to prevent water ingress to the junction. This can be performed on pipe to flange connections in any remote situation with 3” to 15” pipes.
A full demonstration of the operation was performed on 10” pipe using the hydraulic compressor and ram, and sectioned flanges were offered to the audience as proof of the integrity and bond.
Finally, a presentation was made on engineering repair solutions for pipe work and structural beam strengthening. These composite repairs use glass and carbon fibre cloth which is soaked in epoxy and then systematically wrapped around surface-prepared pipes, T-junctions elbows or structural beam sections, to cover and reinforce damaged or thinned areas of pipe or steelwork. The wrapping fibre used has a woven nature and anisotropic strength. Once wrapped, a compression bandage is added and within 24 hrs, the epoxy laden fibre will reach its full cured strength. The wrap system is ideal for situations were emergency or temporary repairs are required, but is often suitable for longer term fix until major maintenance programmes are permissible. ICR are also able to wrap pipes under service and low pressure which are leaking. A flanged threaded plate is fitted into the leak and a hose added to divert the leaking fluid while the pipe and edge of the plate are wrapped in the composite. Once the wrap has cured, the threaded plate can be fitted with a blanking plug to reseal the pipe.
At the close of the industrial visit, the Chairman, Dr Yunnan Gao, presented ICR with a certificate of appreciation. Further industrial visits are planned for September 2019 (NCIMB Microbial Laboratories) and March 2020 (Oceaneering NDT).
The April event was the annual joint meeting with the MCF (Marine Corrosion Forum) where the branch were very
pleased to welcome Scaled Solutions Ltd of Edinburgh, to talk on their recent R&D findings into the performance and optimization of corrosion inhibitors, including those for demanding HP (12,000 psi) / HT (300 C) operations.
(The Scottish Government recently recognised Scaled Solutions’ contribution to Research and Development through the provision of a £2.2M grant award in June 2017, to support R&D in several key areas for the Oil and Gas Production industry. This award, together with significant further investment by Scaled Solutions themselves of £3M, should bring significant cost-saving and corrosion prevention benefits to O&G operations).
It is well known that during qualification of a corrosion inhibitor, it is extremely important to carry out laboratory-based assessments that are prudently representative. However in practice, there are many variables that can contribute to the corrosive nature of a system and it is often costly and time consuming to accurately reproduce all the different field conditions. Because of this, investigations are normally carried out using an iterative screening programme, starting with simple tests, followed by product deselection and then further more complex tests. The simplified screening tests then determine the preferred products and dose rates which can pass to the next stage of testing. It is therefore vital that these initial screening tests are carried out in an appropriate a manner as possible.
Hunter Thomson explained how Scaled Solutions’ ongoing research into seemingly small changes to test methodologies and conditions in these preliminary screening tests, can significantly influence the outcome of screening studies. A range of corrosion inhibitors based on common chemistries have been formulated by them to test these effects more precisely, and their extensive results to date have illustrated the controlling effect of aspects such as pre-corrosion, the impact of the brine chemistry, inhibitor composition, as well as the effectiveness of partitioning for different chemicals, on the performance and relative performance of different products.
Hunter highlighted how relatively small changes in the methodology adopted, can lead to considerable differences in the observed performance, ranking, and outcome of the
pre-screening of corrosion inhibitor chemicals, and that thorough understanding and careful design of corrosion inhibitor screening programmes are essential to eliminating possible errors and test artefacts.
This most interesting presentation generated many questions and proposals for future work, covering topics such as effects of intermittent chemical injection, surface area and scaling.
At the close of the meeting, the chair presented Hunter Thomson with a certificate of appreciation.
Looking further ahead, the branch will be hosting its annual full-day Corrosion Awareness course on 27th August 2019, (via key sponsor Rosen), comprising of a number of lectures/presentations focusing on microbiologically influenced corrosion (MIC) in pipeline systems. This year’s programme will include talks by ROSEN specialists and other visiting speakers, on their MIC Experiences from global operations covering, sampling, analysis, monitoring of pipelines for mic damage, chemical mitigation / cleaning strategies, and finally inspection, modelling and monitoring approaches.
Most certainly this event will provide a very comprehensive introduction to this very significant and often troublesome area of Corrosion Control/Prevention, and the provisional programme can be found on the Institute website.
Full details of future ICorr Aberdeen events can be found on the diary page of the magazine and on the website, or by contacting: ICorrABZ@gmail.com, and all past branch presentations can also be found on: https://sites.google.com/site/icorrabz/resource-center
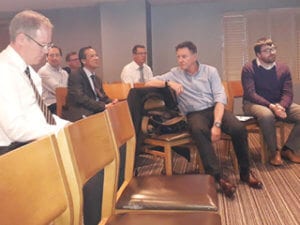
MCF and ICorr Delegates at April Joint Event.

Hunter Thompson of Scaled Solutions Ltd.
Corrosion Engineering Division, Latest News
The Institute of Corrosion is running meetings of both the Corrosion Science Division (CSD) and the Corrosion Engineering Division (CED) as part of the Electrochem 2019 conference, which is being held from 26-28 August at Strathclyde University, as follows:
1. The Corrosion Science Symposium will include presentations on the electrochemical aspects of corrosion science and will cover state of the art developments in fundamental corrosion science. Presentations will be given in on Tuesday 27th and Wednesday 28th August. This symposium will include presentation of the U.R. Evans award to the 2019 winner, Tetsuo Shoji.
2. The Corrosion Engineering Day will take place on Wednesday 28th August only. In the morning there will be a series of invited lectures from experienced practitioners on the theme of ‘Electrochemical Corrosion Monitoring in Industrial Applications’. This symposium will include presentation of the Paul McIntyre award to the 2019 winner, Steve Paterson. In the afternoon CED working group meetings will take place (Coatings, Oil and Gas, Nuclear, CP, Corrosion in Concrete). A day rate option is available on the registration page for people attending the CED meeting only. Attendance at the working group meetings only is free of charge. Please email Nick Smart (nick.smart@woodplc.com) to indicate which working group meeting(s) you plan to attend.
Full details about registration etc. are available at https://www.strath.ac.uk/engineering/chemicalprocessengineering/electrochem2019/
Please note that the early bird registration fees expire on June 21st.
We look forward to seeing you there.