Institute News
The Institute of Corrosion (ICorr) is pleased to announce the launch of a complete suite of digital membership badges, now available to all categories of ICorr members. This includes individual members—Student, Affiliate, Technician, Professional, and Fellow—as well as company members—Sustaining, Gold Sustaining, and Corporate.
These digital badges are designed to recognise and promote the achievements and professional standing of ICorr members within the corrosion prevention and control community. Members are encouraged to proudly display their respective digital badges on professional profiles, websites, email signatures, and marketing materials to visually demonstrate their commitment to excellence and affiliation with the UK’s leading corrosion authority.
ICorr remains committed to supporting and celebrating its community, and this initiative marks another step in strengthening the visibility and value of ICorr membership in both industry and academia.
For more information or to download your digital badge, please visit Members Area.
Institute News, Latest News
The Engineering Council is delighted to announce that the Institute of Corrosion (ICorr) has become a licensed professional engineering institution with approval to assess its members for professional registration as Chartered Engineer (CEng), Incorporated Engineer (IEng) and Engineering Technician (EngTech) on the Engineering Council’s national Register.
Founded in 1959, ICorr has been a Professional Affiliate since 2001. ICorr serves the corrosion science, technology and engineering community in the fight against corrosion. Central to this is ICorr’s promotion of good corrosion management practice, the advancement of corrosion control measures and awareness at all stages of design, fabrication and operation across various sectors.
Engineering Council CEO, Paul Bailey, said: “The Licensed Professional Engineering Institutions represent engineers and technicians from across all industries. As the UK’s leading professional organisation dedicated to the science and engineering of corrosion control and prevention, I’m delighted that members of the Institute of Corrosion will now have the opportunity to have their engineering competence and commitment to upholding safe, ethical and sustainable practices formally recognised. The award of the Engineering Council licence recognises the Institute’s strong commitment to promoting best practice and standards development in the field of corrosion management and we look forward to working with ICorr in the promotion of professional excellence.”
ICorr President, Dr Yunnan Gao, commented: “The Institute of Corrosion is honoured to have been granted licensed status by the Engineering Council, enabling us to independently assess and recommend our members for inclusion on the Engineering Council’s Register at all levels: EngTech, IEng and CEng.
This significant milestone reflects the increasing recognition of corrosion science and engineering as essential to the integrity, sustainability, and safety of the built environment. It further reinforces ICorr’s vision to advance the science and engineering of corrosion prevention for the public benefit. We look forward to playing a greater role in supporting professional excellence and upholding the highest standards within the engineering community.”
Further information on currently licensed professional engineering institution can be found on the Engineering Council website
For EngC Registration through ICorr:

Please contact: Anthony Setiadi (Chair)
Email: ECReg@icorr.org
ICorr Training:, Institute News
Powder coating is a type of coating that is applied as a dry, fine powder to produce high-quality and durable finishes. Unlike conventional liquid coatings and paints, which are typically applied via a brush or roller, powder coatings are applied as a free-flowing powder that streams smoothly and evenly.
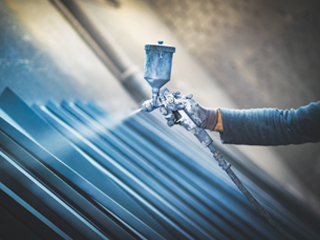
This application can either be conducted through electrostatic spraying or a fluidised bed dipping process, followed by a necessary heat (or UV) curing process.
Since their early development in the 1940’s, powder coatings have come to take large swathes of the protective coatings industry by storm. Today, they enjoy a dominant position in a range of markets (including architectural, industrial and transport), and this dominance is only predicted to intensify. Indeed, whilst the current global powder coatings market stands at a significant $15.2 billion in 2024, this is projected to grow by a whopping $9 billion to reach $24.26 billion in a mere eight years’ time (Chemicals & Materials Industry – Fortune Business Insights).
The soaring popularity of powder coatings can be attributed to their many advantages over alternative protective coating materials. Firstly – and perhaps most importantly, given our ongoing climate crisis – powder coatings are significantly more sustainable than their traditional liquid counterparts.
This is in large part due to their exceptionally low (or often
non-existent) Volatile Organic Content (VOC), eliminating the health hazards and air pollution associated with solvent emissions. Additionally, the limited overspray powder produced in the application process can be recycled and reused, ensuring minimal waste.
Powder coatings are often more economical options than their liquid counterparts. Whilst initial set-up costs can be high, their transfer efficiency is streaks ahead of traditional liquid paint methods, reaching an impressive 95% when applied using the fluidised bed technique. Furthermore, the equipment used for powder coating requires relatively minimal maintenance, making it more convenient and cost-effective.
Remarkably, the huge environmental and economic benefits powder coatings incur do not lead to diminished performance. In fact, many powder coatings – when applied as a single layer and cured by heat – provide comparably exceptional durability, chemical resistance, toughness and flexibility. Taking all this into account, it appears evident that powder coatings constitute the future of the protective coatings industry.
It is in this context that Corrodere Academy is proud to announce its new Powder Coatings application course. Expertly crafted, engaging, and informative, the course is designed to ensure high-quality training is available within the industry – an availability that is essential as the powder coatings market continues to boom. Following the course’s launch, we sat down with Brendan Fitzsimons – Corrodere’s Technical Director and leading industry expert – to hear his thoughts.
- What Motivated Corrodere to Design the Powder Coatings Course?
Our primary goal is to address the rapidly growing demand within the industry, driven in large part by increasing sustainability concerns. As the industry expands, more and more manufacturers are looking to bring powder coating capabilities in-house. However, the surge in demand has outpaced the availability of skilled professionals. Many companies have invested in powder coating units but find themselves without the trained staff necessary to operate them effectively. This is where we step in, providing the high-quality training needed to equip these companies with the expertise required.
- Who is This Course Targeted At?
This course is primarily targeted at powder coating applicators and associated workers involved in the powder coating process. Our training is designed to be highly practical and hands-on, focusing on the real-world skills needed on the job rather than delving too deeply into technical or scientific theory. The theoretical components of the course are digestible, ensuring applicators gain the necessary knowledge without being overwhelmed by complex concepts.
The course will also be helpful for powder coating technical and sales staff from powder suppliers and equipment suppliers.
While the applicators are the primary recipients of this training, it’s essential for companies to recognise that powder coating is a team-driven process. From pre-cleaning to application, each step requires careful coordination and expertise. Therefore, it’s crucial for companies to invest in training across the entire team, ensuring that every stage of the process is executed with precision – a need our course is designed to fulfil.
- Why Should Industry Professionals Take the Powder Coatings Course?
As the powder coatings market continues to boom, skilled application of powder coatings is an increasingly vital proficiency for anyone in the industry. Corrodere’s course ensures that students fully understand the many stages and intricacies of the powder coatings process, verifying their competence to carry out this high-skilled work effectively
and safely.
For employers, offering the course to staff defends against potential costly coating failures by ensuring application is done correctly, first-time around. Investing in training is also a way to boost job satisfaction (and, by extension, job performance), ensuring employees know they are rightly perceived as an invaluable resource. Any registered Train the painter company that is engaged in powder coating application can – and should – deliver the course.
- How Valued do You Foresee the Powder Coatings Course Being by the Industry at Large?
Ultimately, we foresee our powder coatings course becoming an industry norm. The benefits of the course are simply innumerable for applicators, companies and clients alike. Applicators benefit from verifiable expertise and enhanced confidence in their work; companies benefit from well-trained staff and an elevated reputation as a consequence of staff investment; clients benefit from knowing they are enlisting highly qualified trade personnel. Indeed, the failure of powder coatings can be costly – Corrodere’s course (the only one of its kind) ensures that rather than relying on reputation, companies and clients alike can trust their powder coating Applicators to have certifiable, accredited skills and expertise.
- Who Endorses the Course?
We’re delighted to say that the British Coating Federation (BCF) has endorsed the programme. Their endorsement highlights the high-quality and necessity of the course, and we’re excited to be working with them.
The Powder Coating Application course is available globally through the Corrodere Academy’s Train the Painter programme. To find out more, please get in touch with the team at.
Contact: Email: lucy@corrodere.com Tel: +44 (0) 1252 732 236
Company Membership, Institute News
Wood is very proud to become a new sustaining member of the Institute of Corrosion.
About Wood
Wood is a global leader in consulting and engineering, delivering critical solutions across energy and materials markets. They provide consulting, projects and operations solutions in 60 countries, employing around 35,000 people.
It’s team of integrity management specialists works with energy and industrial operators to keep assets safe, reliable and efficient throughout their lifecycle.
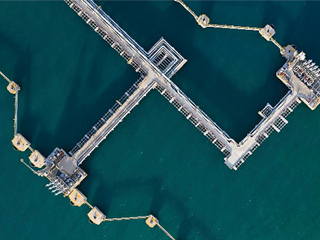
Asset Integrity Solutions
Whether it’s corrosion analysis and control, cathodic protection, integrity management, risk assessments or maintenance planning, Wood aims to identify potential issues and implement targeted strategies to improve the performance and longevity of energy and industrial assets.
Expertise You Can Trust
The Wood team has a proven track record with numerous global majors and a strong commitment to innovation, ensuring its clients benefit from the latest technologies and industry best practices.
Comprehensive Lifecycle Support from Initial Design to Decommissioning
Wood works across every stage of the asset lifecycle using a holistic approach, ensuring to anticipate and address challenges before they become problems.
Through partnering, its clients gain a trusted advisor committed to their long-term success.
Advanced Technology to Identify
Risks Early
Wood uses digital tools, data analytics and predictive maintenance techniques to identify and mitigate risks early, reducing costs and improving operational efficiency. Being vendor-independent, its clients can have the confidence that their assets are managed using the best available technology.
For example, the ECE® (Electronic Corrosion Engineer) corrosion analysis and materials selection software is the leading tool to provide realistic corrosion modelling and lifecycle cost assessments calibrated to actual field data.
Global Reach with Local Expertise
With a presence in key markets around the world, Wood combines global reach with local expertise. By understanding the specific challenges and regulations of each region, it is able to provide solutions that are both globally informed and locally relevant, ensuring the best possible support, no matter where assets are located.
Sharing Our Knowledge
Wood regularly shares its knowledge at industry events in committees and online training.
To join its mailing list or to watch its on-demand webinars, visit: woodplc.com/webinars
To learn more about corrosion and
integrity management please visit us at:
woodplc.com/integrity
Wood assists all to stay up-to-date and earn professional development hours too!
Company Membership, Institute News
New Corporate Member – ICorr Welcomes Hempel: Helping Shape a Brighter Future with Sustainable Coating Solutions.
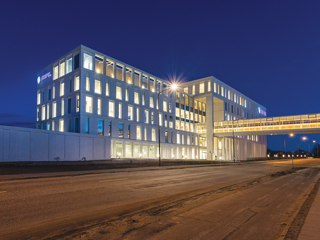
Shaping a Brighter Future
Hempel is a global supplier of coatings across industries.
From bridges and ships to wind turbines and homes, Hempel’s products can be found in almost every country, protecting the world’s buildings, infrastructure and other assets from corrosion. Hempel coatings are essential to their customers’ businesses. They help minimise maintenance costs, improve aesthetics, reduce waste and increase energy efficiency in the operation of assets. They extend the lifetime of the assets they protect – helping lower the asset’s environmental and carbon footprint across its entire lifecycle.
Hempel was established in Denmark in 1915 and today employs people across the globe. It’s headquartered in Kongens Lyngby, near Copenhagen, Denmark.
For The Wider Good
Hempel is majority-owned by The Hempel Foundation, which ensures a solid economic base for the Hempel Group and supports cultural, social, humanitarian and scientific purposes around the world.
In 2023, The Hempel Foundation donated €23 million to development initiatives in the fields of education, biodiversity and science.
Committed to Sustainable
Development Goals
Hempel are committed to the UN Sustainable Development Goals. The UN SDGs are integrated and indivisible, and our Hempel goals work in a holistic way to support them.
-
We are reducing CO2emissions in our own operations and in our value chain and switching to renewables.
-
Our products contribute to a more sustainable and resilient infrastructure.
-
We are pursuing resource efficiency and circularity and reducing harmful substances.
-
We are committed to health and safety and the promotion of diversity and inclusion.
-
We promote ethical behaviour and good environmental practices in our supply chain.
- We collaborate widely and pursue effective partnerships.
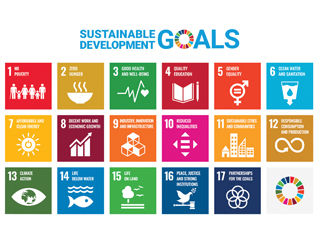
Sustainability at the Heart of Business
Sustainability leadership is a key pillar of Hempel’s Double Impact business strategy. For Hempel, sustainability leadership means being a frontrunner within the paints and coatings industry by enabling customers to meet their sustainability ambitions.
To achieve on these ambitions, Hempel works dedicatedly on sustainability initiatives, with a focus on reducing its environmental footprint, enhancing its social impact and maintaining its strong corporate governance standards.
Liquid Engineering – R&D
Hempel strives to be the best in the business – and that means always looking for innovative ways to improve coating performance, as well as new ways for coatings to improve the world. With R&D centres across Europe, the Middle East, Asia and America, their R&D teams work with customers, research institutes, suppliers and other industries to push the boundaries of what coatings can do – always with the aim of improving customers’ business performance.
-
Hempel’s R&D work Research into the latest paint technologies
- Developing new customer-focused products and solutions
- Partnering with customers to tailor solutions
- Reducing the environmental impact of coatings
-
Increasing the sustainability value derived from the use of coatings, including extending the lifetime of assets and increasing the energy efficiency of operating assets
Focuses on Driving Innovation in Protective Coatings
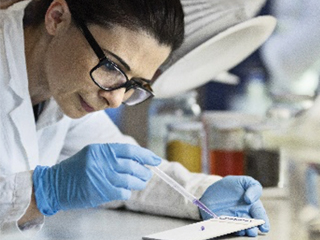
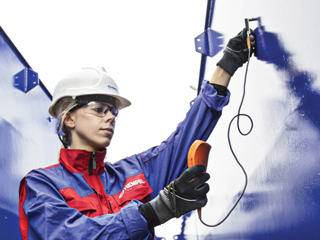
As a global supplier of coatings across industries, Hempel develops advanced coatings solutions to protect assets, reduce maintenance and enhance performance. One leading example is ‘Avantguard,’ a patented technology that sets new standards in corrosion protection.
https://www.hempel.com/inspiration/sustainability
For over 10 years, this innovative coating solution has extended the lifetime of steel structures across a wide range of applications, from wind towers and bridges to airports and skyscrapers. It not only prolongs the lifespan of assets but also simplifies application, reduces maintenance costs and lowers CO₂ emissions. It’s the ideal corrosion protection solution for any forward-thinking asset owner, consulting engineer, contractor or applicator.
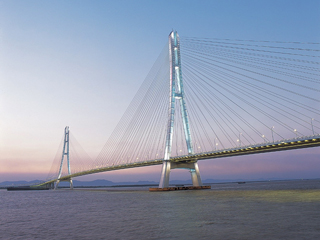
Avantguard is the world’s first zinc-rich primer to fully utilise its zinc content by activating all three methods of corrosion protection: the barrier, the inhibitor and the galvanic effect.
With its unique properties, Avantguard ensures superior durability and reduced environmental impact in addition to its easy application, offering fast drying, fewer coats, and an excellent crack-resistant finish.
And with the recent launch of Avantguard 750 Pro, setting a new industry standard for corrosion protection and building on over a decade of Hempel’s patented Avantguard technology, Hempel reaffirms its dedication to sustainability and high-performance coating systems.
Contact
For more information, visit Hempel’s website www.hempel.com or reach out to the team at hempel@hempel.com
Photo: Hempel Headquarters – Copenhagen, Denmark.
Figure 1. UN Sustainable Development Goals.
Photo: Hempel R&D work.
Photo: Hempel Bridge Protection.
Institute News
Submitted by: Stephen Tate, Immediate Past President.
Photos: Failure of Lamppost Cover Around a Non-Carbon Steel Fastener Spotted in Inverness Scotland.