The cart is empty!
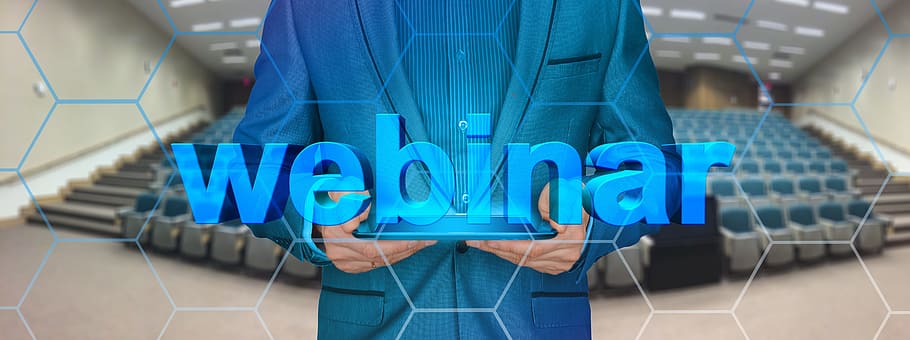
Corrosion Protection – A Week of Webinars
Bringing the corrosion conversation to you
After the huge success of the week of webinars to combat corrosion, the Marine Corrosion Forum and the Institute of Corrosion are collaborating once more to bring five more exceptional webinars into your homes and places of work, as we discuss some of today’s corrosion protection issues.
These webinars, presented by some of the world’s leading corrosion experts, will follow the same format as before: one each day for five days, each presented at a time to allow as many people as possible to attend. You’ll need to be quick to register, though – there is a limit of 200 people for each webinar, and places will be allotted on a first-come-first-served basis.
Online delegates to this series of webinars are in for a real treat – with a big focus on offshore wind and other renewables, and a ‘dip-in/dip-out’ timetable that allows you to attend the webinars individually without needing to commit to attending all five. Oh, and registration for these corrosion protection webinars is free.
Before a summary of each webinar, let’s introduce the presenters – it’s quite a line-up.
Dr Roger Francis
Dr Roger Francis is one of the UK’s leading experts in corrosion-resistant alloys – both stainless steels and copper-based. Director at RF Materials, Dr Francis won’t mind us telling you that he has amassed four decades (and counting) of experience in areas that include marine, oil and gas, chemical and process, power, desalination, and mining. He has authored six books, and edited several more, as well as publishing over 80 technical papers. His consultancy work includes failure analysis, materials advice, and training in various aspects of corrosion. A founder member of the Marine Corrosion Forum and a Fellow of the Institute of Corrosion, Roger never fails to deliver an informative and enjoyable paper.
Dr Adnan Syed
With a PhD in Energy Materials, Dr Adnan Syed is currently a Research Fellow at Cranfield University. There, he is involved in the field of high-temperature material degradation and investigating the effects of environment on the static and stress corrosion life of alloys used for gas turbine blades. This includes the use of thermodynamic software for better understanding of the corrosion mechanisms and advanced microscopy techniques for the alloy’s microstructure details. His PhD title was ‘Fireside corrosion study of superheater materials in advanced power plants’. Dr Syed’s extensive career experience, includes working for organisations to provide chemical solutions to R&D and technical teams via Failure Mode Effects & Analysis (FMEA) toward the development of products and processes.
Lars Lichtenstein
You couldn’t wish for a more accomplished corrosion mitigation voice from the world of renewables, especially offshore wind. Lars Lichtenstein is the lead principal specialist within Renewables Certification for corrosion protection issues at DNV GL – the responsible expert for the DNVGL-RP-0416 corrosion protection for wind turbines. Extremely influential in setting and interpreting DNVGL codes and rules in this sector, you’ll discover that Lars is also an extremely competent and accomplished presenter.
Brian Wyatt
Just when you thought it would be impossible to add to the expertise of our presenters, we bring you Brian Wyatt. Members of the Institute of Corrosion will recognise Brian as a past president of ICorr and Director at Corrosion Control Limited. An acknowledged expert in cathodic protection, Brian has been heavily involved in transferring best practice from the oil and gas sector to the offshore wind sector and is active in the preparation of the new EN ISO 24656 standard “Cathodic Protection of Offshore Wind Turbine Structures”.
Andrew Woodward and Chris Matthews
The week starts strongly, and it certainly doesn’t fizzle out. The last of the week’s webinars delivers a ‘two-for-the-price-of-one’ experience (except, of course, there is no cost – all the webinars are free).
Andrew Woodward is Marketing Manager at Connector Subsea Solutions including MORGRIP. Andrew has a BEng and an MSc in mechanical engineering from Aston University. Andrew has over 10 years of experience in technical sales and estimation in specialist applications and joined the MORGRIP team in 2016.
Joining Andrew ‘on stage’ is Chris Matthews, Project Engineer at Subsea……
Chris Matthews joined the MORGRIP team in 2014 shortly after finishing a BEng in Aerospace Systems Engineering at Coventry University. After a short period working with standard products Chris was engaged in a high-profile project for Mechanical Connectors for Deep Water Repairs which lasted 2 years. After that Chris was a leading figure on the engineering team developing the new MORGRIP CLiP Connectors which are the subject of today’s presentation.
The agenda for this week of webinars
Without further ado, let’s take a glimpse at each of the webinars. Each will be a one-hour presentation by the subject expert. A Q&A session via the chat box immediately follows the presentation.
Improving the Corrosion Resistance of Duplex Steel Welds (Dr Roger Francis)
Monday 6th July 2020, 12pm BST
Register for this webinar here
Modern duplex stainless steels have been in common use since the early 1980s, and how to weld these alloys satisfactorily is well understood. Despite this, corrosion failures of welds still occur. This talk will discuss the important parameters to produce satisfactory welds in duplex stainless steels. There are further things that can be done to improve the corrosion performance of duplex welds, and these are discussed along with test data. It is important that testing over and above that in ASME IX is carried out on duplex weld Procedure Qualification Records (PQRs) and some suitable tests are proposed. The corrosion resistance of welds and parent metal to different sorts of corrosion will be discussed.
Hot Corrosion Mechanisms for Gas Turbines (Dr Adnan Syed)
Tuesday 7th July 2020, 12pm BST
Register for this webinar here
Hot corrosion mechanisms were first proposed more than half a century ago, but we are still learning about them and they continue to be a focus for manufacturers of aero and industrial gas turbines.
The understanding of corrosive salt and target alloys are both crucial topics to enable improved mechanisms. Corrosion mechanisms vary due to the composition of the alloys and deposit salt chemistries.
The concept of acid and basic flux on the alloy surface due to induced deposits on the alloy’s surface is also well defined; however, further investigation is still required.
Along with laboratory corrosion experiments, the use of thermodynamic software is a key tool to help identify the likely phases formed, which in turn enables a better understanding of the mechanisms involved.
The talk will include the possible hot corrosion mechanisms occurring in the gas turbine combustion environment, and support some of the challenges the industry is facing in its understanding and managing of turbine component degradation. The talk will also present the laboratory setup for hot corrosion testing and techniques used for evaluation of material performance.
Improvements of the DNVGL-RP-416 and DNVGL-RP-B401 – Upcoming Revisions (Lars Lichtenstein)
Wednesday 8th July 2020, 12pm BST
Register for this webinar here
This is a must-attend webinar for those working in the wind turbine industry. You’ll receive the inside track on material selection for bolts and stainless steel, and the boundary conditions that should be considered.
The recommended practices issued by DNV GL on corrosion protection for wind turbines are being reviewed internally. Learn what the items and considerations under review are, and become updated on how the process of review is used to address and improve the overall quality of corrosion protection for offshore wind.
The current key DNV GL documents for corrosion mitigation and CP in this sector are DNVGL-RP-0416 and DNVGL-RP-B401. Formally, DNVGL-RP-0416 is issued from Renewables Certification, part of the energy business, while DNVGL-RP-B401 is owned by the oil and gas business. Therefore, this presentation will mainly deal with the items and considerations being dealt with for the revision of DNVGL-RP-0416, but relevant topics in relation to DNVGL-RP-B401 can also be addressed and discussed.
Since 2016, when DNVGL-RP-0416 was first published, these recommendations were applied to numerous offshore wind projects. We have been part of the certification process for many of these projects and could gain experience and feedback on the content we have issued. Generally, there has been positive feedback, but some guidance lacks sufficient detail. Some of these areas need to be addressed to improve the overall quality of corrosion protection for offshore wind.
Several relevant standards have been revised since 2016 (e.g. ISO 12944 or ISO 2063), new standards like VGB/BAW have been introduced, and new ISO standards are currently being written in several working groups. Improvement of the guidance given is needed and possible. We want to address the most relevant items with new revisions of our RPs.
This seminar will provide more guidance on the useful coating lifetime as introduced in DNV-OS-J101:2011 for the first time, and the relation with fatigue calculation and surface preparation. What level of quality is needed at the end of the lifetime? How much effort shall be put into inspection and repair of 15-year-old+ coating systems? You will gain insight on material selection for bolts and stainless steel, as well as what boundary conditions should be considered. This seminar will also study the issue of coating breakdown factors with regards to CP system calculation and on currency drain of buried structures. The revisions of the documents are not yet finished, and therefore input from this event will be able to influence the development of future recommended practices.
Cathodic Protection of Offshore Renewable Energy Infrastructure (Brian Wyatt)
Thursday 9th July 2020, 12pm BST
Register for this webinar here
External surfaces of offshore structures, including offshore wind turbine foundations and tidal/wave energy structures are routinely protected from corrosion by cathodic protection [CP] using aluminium alloy galvanic anodes. Design codes for this are provided by several sources; the most commonly used for offshore wind applications being DNVGL-RP-B401.
These codes have been produced primarily for jacket structures used in deep water for oil and gas developments. They are inadequate for structures required for offshore energy infrastructure such as offshore wind turbine monopile [MP] foundations, tidal turbines, or wave generators – all of which need to be installed in near-shore shallow water environments. For these conditions, there are special considerations over and above those defined in these codes, notably the impacts of higher tidal flow, a greater proportion of the shallow structures being in the tidal zone and of wave action. All result in high levels of oxygenation at the steel/water interface which demand more robust CP designs, both in mechanical and electrochemical terms. The nature of the support structures, and limited scope for lower-cost onshore anode installation, also lead to challenges to uniform anode distribution, particularly on MPs.
Although DNV GL has addressed some of these issues in its DNVGL-RP-0416, written specifically for offshore wind applications, it has not addressed all of the environment issues, and the requirements remain largely biased towards the use of RP-B401 for CP design.
A new International Standard, EN ISO 24656 ‘Cathodic Protection of Offshore Wind Turbine Structures’ is under development to address these issues more fully. It will soon be published for public comment. It will reflect a significant change in the design process for cathodic protection, to reflect the particulars of offshore wind foundations and their environments.
This seminar concentrates on these additional considerations for the design of external CP for near-shore offshore energy infrastructure. It also, briefly, discusses the special and different requirements for internal CP of wind turbine monopiles.
Use of CRAs in Subsea Pipelines and Repair of Clad Pipeline Connections (Andrew Woodward and Chris Matthews)
Friday 10th July 2020, 12pm BST
Register for this webinar here
Since 2009 the MORGRIP team has been engaged with major operators to develop a mechanical connector solution specifically designed to meet the unique challenges of Clad and Lined Pipeline systems. A traditional mechanical connector seals on the outer diameter of the pipe and is used as an alternative to welding for straight cut pipe ends. For a clad or lined pipe this type of connector does not adequately protect the pipe end and parent pipe from the corrosive attack of the aggressive sour line media.
The CLiP Connector was developed over 2 phases of a Joint Industry Project part funded by Chevron and Woodside. The aim of the JIP was to take the existing MORGRIP connector technology and integrate a mechanism to protect the exposed end of a clad pipeline from the aggressive line media after installation.
The seal takes advantage of the corrosion resistant and ductile properties of Alloy 625 when subjected to specially controlled heat treatment as well as extensive testing and track record of graphite in order to create a seal module that conforms to NACE MR0175 / ISO15156-3. The seal forms around all pipeline manufacturing tolerances and even localised irregularities such as internal weld seams. The seal can be easily integrated into existing mechanical connector configurations and is able to be adapted for both diver installed and remote repairs.
The technology qualification was completed to DNVGL-RP-A203 through a combination of analysis, 3rd party material testing, component testing and culminating in full scale testing of a production unit. This resulted in the award of a DNVGL Type approval for the product range in accordance with the requirement of DNVGL-ST-F101 for submarine pipelines and DNVGL-RP-F113 recommended practice for pipeline repair.
Don’t miss out on these webinars
We’re anticipating strong demand for these extremely current webinars. Not only because of the subject matter, but because of the authority of the presenters. Don’t miss out – register now. As the year progresses, we plan to bring you more events that bring the corrosion conversation to you –another example of the benefits of membership of the Institute of Corrosion.
For details about membership of the Institute of Corrosion, visit our membership page.