The cart is empty!
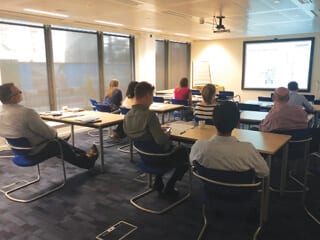
You Can’t Keep Innovative Young Engineers Down
Could you solve this case study and become a big winner?
The young engineers in the Institute of Corrosion’s Young Engineer Programme are an innovative bunch. There was no way that the coronavirus lockdown and curtailing of mass gatherings was going to stop them in their tracks.
Instead of in the elegant Royal Over-Seas League club in London, these intrepid young engineers gathered around their computer screens at home to learn of the 2020 Case Study that will be used to determine which group of young engineers will be the winners of this year’s star prize. It was the first time that an ICorr Young Engineers group had met online, but was so successful that it is unlikely to be the last.
2018’s Winning Young Engineers group whet appetites for success
With an appraisal of their winning case study from 2018, Caroline Allanach, Danny Burkle and Tim Evans whet the appetites for success of the young engineers in attendance online during the evening.
The insight they provided as to how they approached their task, and a critical assessment of their reaction and solution to the failure that occurred was both informative and entertaining. So, too, was their description of the prize they won – a tremendous trip to the 2019 NACE Conference in Nashville.
A corrosion conundrum is this year’s case study
There are seven participating groups in this year’s Young Engineer Programme case study, and they have been given quite a conundrum to unravel.
The case study was presented by Steve Paterson, from Arbeadie Consultants Ltd., who has a career of corrosion experience to draw on. He hasn’t made it easy for this year’s programme participants. Here is the scenario he has set:
- Several leaks have been identified in the titanium piping in an onshore desalination plant
- This plant is used to remove salts from mono-ethylene glycol
- The plant is also used for hydration and corrosion control in gas pipelines from three offshore fields
At the end of the presentation, the 32 young engineers were posed with the problems they must work to overcome, which include:
- How to perform a corrosion risk assessment to determine that the plant is safe to operate
- Recommending alternative materials to use
- Identifying what mitigation options could be used to prolong the life of this section of the desalination plant
- Identifying the root cause of the corrosion
Online meetings can get lively!
The young engineers in this year’s intake come from 19 companies, and their specialities include mechanical and materials engineering, welding, materials, and more. With such diversity, you might expect a lively meeting when in a meeting room. It was hard to know what to expect online, though.
The discussions that followed the presentation of the case study proved that no matter how we get together, when there’s an interesting and provocative scenario put forward, online events can be just as lively as in-person meetings.
The range of experience and specialties were certainly put to the test, and the question and answer session proved to be the first opportunity for ideas and complexities to be explored.
In brief, a fruitful, useful and exciting meeting, aptly brought to a close by Trevor Osborne, a past President of the Institute of Corrosion, and Managing Director of Deepwater Corrosion services (UK) Ltd.
The big wait begins!
And so, the big wait begins. It will be several months before we learn which group of young engineers will be this year’s winner.
The groups now undertake further investigation, collaborating behind the scenes and aided by four more lectures, and the help of a mentor assigned to each group, before presenting their case studies in November.
Could you be a future winner in the Young Engineer Programme?
Watch this space! The Young Engineer Programme is held biannually. To learn how you could become a winner, visit our YEP pages or email the Institute of Corrosion at admin@icorr.org.